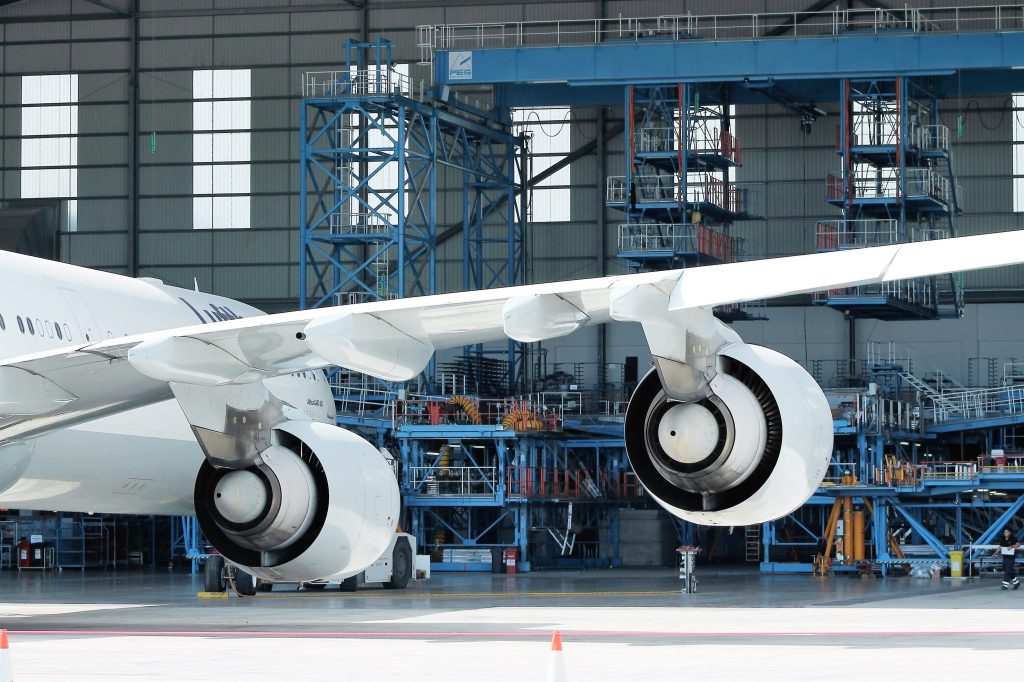
What Is Predictive Maintenance for Aviation?
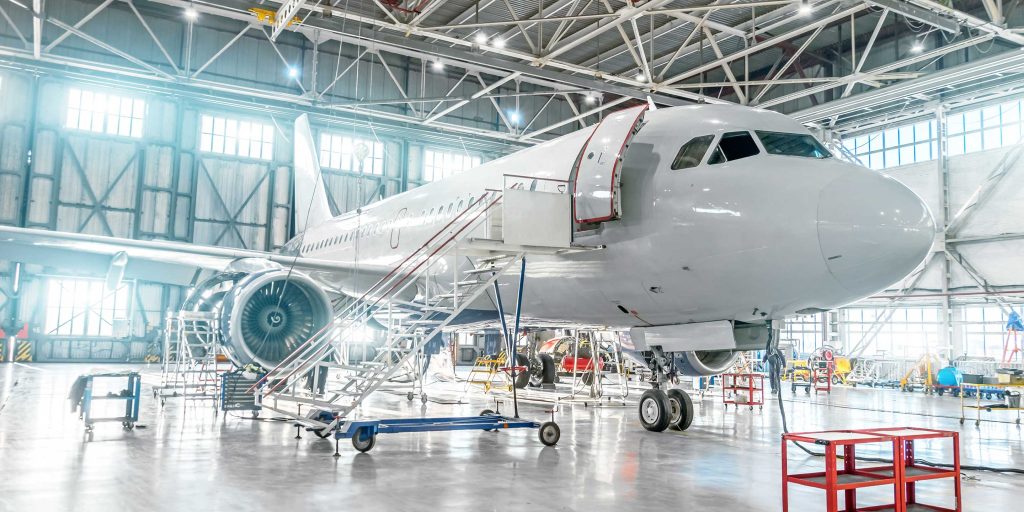
Predictive maintenance is a strategy for maintaining equipment and systems that use data and analytics to predict when an item is likely to fail. This is in contrast to traditional “reactive” maintenance, in which equipment is only fixed or serviced after it has broken down, or “preventive” maintenance, in which equipment is serviced on a regular schedule, regardless of whether it needs it.
Predictive maintenance aims to reduce the frequency of equipment failures and associated costs, such as downtime and repair costs. Therefore, it is often used in manufacturing, transportation, and energy industries, where equipment failure can be costly and disruptive.
To implement predictive maintenance, data is collected from the equipment, such as vibration readings, temperature readings, or oil analysis, which is then analysed in real-time or periodically to detect patterns or anomalies that may indicate an impending failure. By performing maintenance before the equipment actually breaks down, the company can avoid unplanned downtime and reduce overall maintenance costs.
It is also commonly used for machine learning algorithms to predict failure based on historical data and utilise IoT sensors to gather data from the machines.
Relationship Between Predictive Maintenance and Chemical 4.0
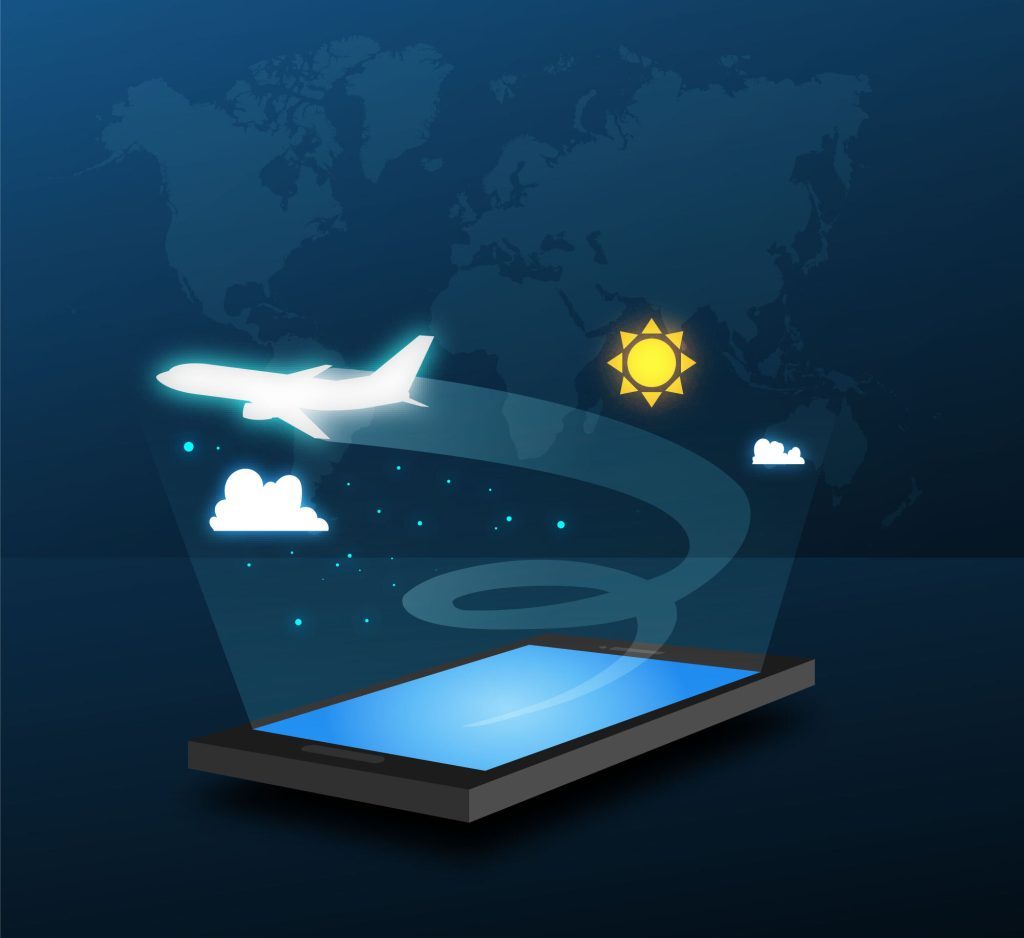
Chemical 4.0, also known as Industry 4.0, is a term used to describe the integration of advanced technologies, such as the Internet of Things (IoT), artificial intelligence (AI), and machine learning (ML), into the chemical industry.
Predictive maintenance is one aspect of Chemical 4.0, as it uses advanced technologies such as IoT sensors, AI and ML to predict when equipment is likely to fail. These technologies empower automated damage recognition that allows aviation companies to perform equipment maintenance before it breaks down, avoid unscheduled removals, and increase time on the wing.
Advantages of Predictive Maintenance
Predictive maintenance is vital for many reasons.
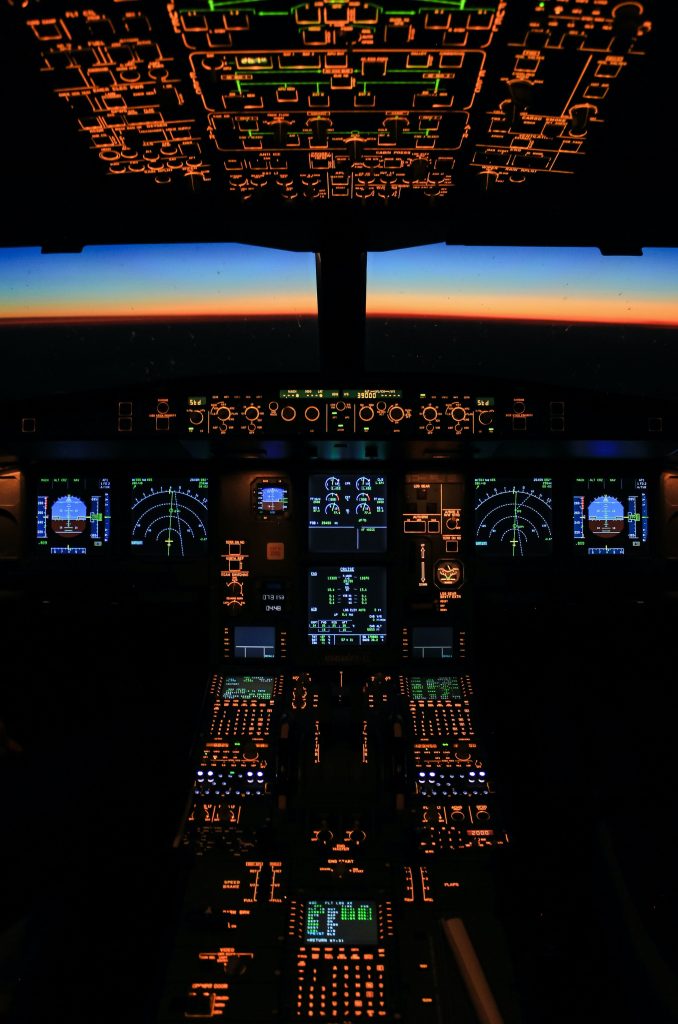
- Cost savings: By performing maintenance before equipment fails, companies can avoid unplanned downtime and the associated costs, such as lost productivity and repairs. Predictive maintenance can also reduce the overall maintenance cost since the equipment is only serviced when needed.
- Increased uptime: Predictive maintenance can help increase equipment uptime by identifying and addressing issues before they cause a failure. This can improve productivity and reduce the risk of costly downtime.
- Safety: Predictive maintenance can aid in improving safety by identifying and addressing potential hazards before they cause an accident
- Equipment optimisation: Predictive maintenance enables optimised equipment performance. Identifying and addressing issues early extends the longevity of the equipment, improves energy efficiency, and reduces emissions.
- Data-driven: Predictive maintenance allows for a more data-driven approach to maintenance, providing insights into how equipment is performing and identifying trends that can be used to improve processes and prolong equipment life.
- Better decision-making: It also allows organisations to make informed decisions about their maintenance activities and budget allocation. This can lead to better overall planning and execution.
Overall, it is an essential strategy for maintaining equipment and systems. It can help companies save money, increase uptime, improve safety, optimise equipment performance, and make more informed decisions.
Predictive Maintenance Gaining Traction
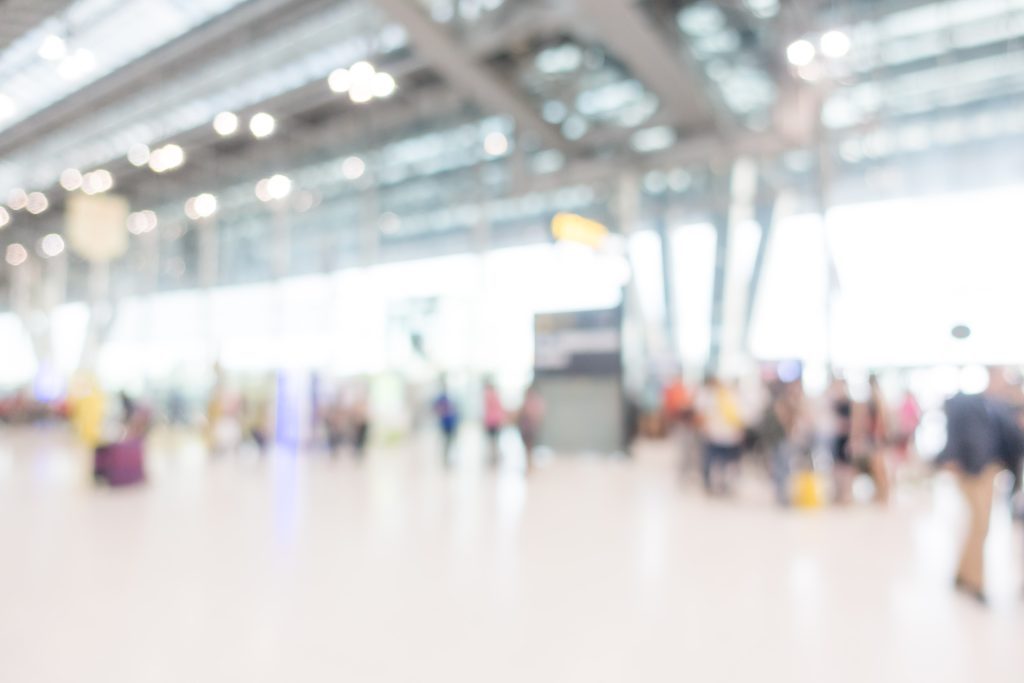
Industry recovery has spurred interest in predictive maintenance—with the international border opening and aviation activities returning to normal, and the industry is seeing more airline customers who are keen to incorporate it into their renewed or new maintenance-by-the-hour contract for their critical aircraft components.
This may prompt the acceleration of predictive maintenance, which prior to the pandemic, was struggling to gain popularity with many airlines outside of engine applications. However, estimates now show that about 50 airlines are covered by true predictive maintenance, i.e., maintenance following predictions. In addition, many aircrafts have started utilising Original Equipment Manufacturer’s (OEM) predictive maintenance. While these numbers are not as impressive as one would like them to be, they still present a stark improvement from the pre-pandemic era.
Hurdles to Predictive Maintenance
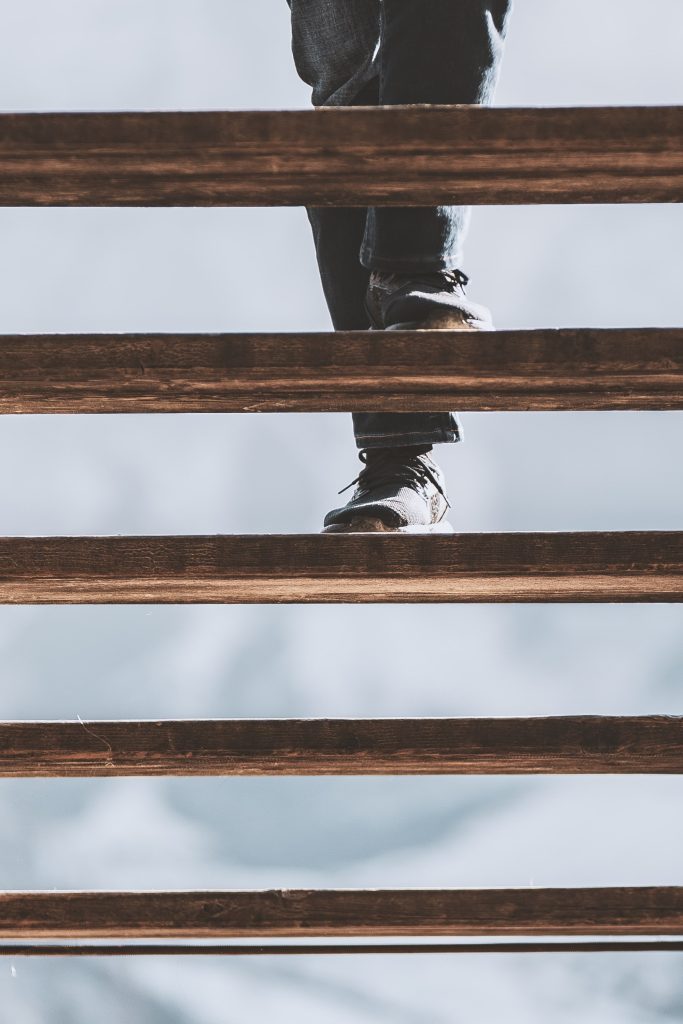
This lack of data sharing can also lead to other issues. For example, in some cases, airlines may not be able to access the operational data they need to use predictive maintenance technology, while at other times, they may be hesitant to share data with third-party MRO providers due to the fear that it would benefit their competitors as much as it would benefit themselves.
By running machine learning algorithms on multiple datasets from various operators, it would be possible to develop algorithms without having direct access to another operator’s data. This will allow companies to maintain their data security, anonymously use their data, and still develop powerful algorithms that could be used across multiple operators.
For airlines to fully adopt predictive maintenance, they must be willing to make changes to their traditional maintenance processes and replace serviceable components that the algorithms suggest should be replaced, even if they do not appear to be faulty. This is because the algorithms use data to predict when these components are likely to fail. Failure to do so could result in increased costs or downtime later on, as equipment failure is more expensive to fix and disrupts operations more than preventative maintenance. Ultimately, the probability of this change relies on the customer’s openness to adopt innovative solutions and willingness to change their traditional processes if the solutions show valuable results.
To test the validity of an action, companies have to value predictions by effectively collaborating with each other.
Understanding the Use Cases of Predictive Maintenance
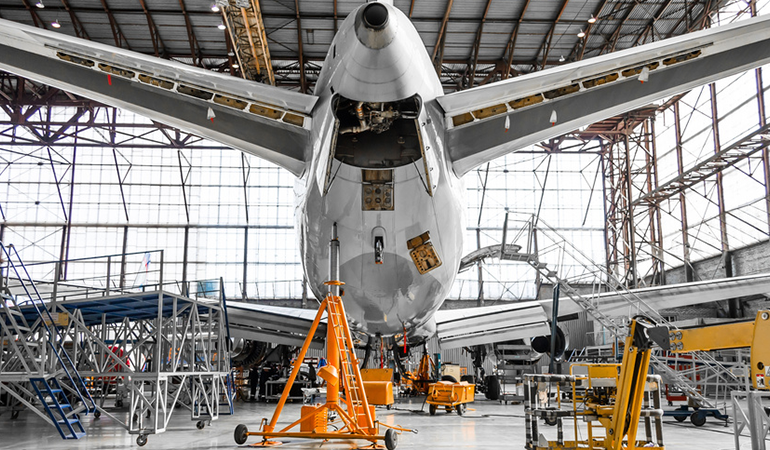
Predictive maintenance technologies help improve the efficiency and reliability of aircraft maintenance by using artificial intelligence and machine learning to analyse sensor data from aircraft systems to predict when maintenance will be needed. By identifying potential issues early on, the tools allow scheduled maintenance to be performed before a breakdown occurs, reducing costly unplanned downtime and increasing aircraft availability.
One such technology has enabled a $4,000 savings on annual expenses linked to a specific system, avoiding troubleshooting labour and saving fuel. Another software uses continuous aircraft sensor data to calculate health metrics of various components each flight and, with the help of algorithms, uses historical data along with AI to predict potential issues on aircraft. This technological invention has tremendously helped reduce unplanned ground time and optimise inventory planning and troubleshooting times for cargo cooling systems.
Many other companies also use predictive maintenance through their in-house component management product. In addition, they plan to integrate engine health management and airframe MRO systems into their one-stop portal for MRO services for better maintenance of the components.
Some additional common use cases of predictive maintenance are mentioned below:
- Monitoring equipment for signs of wear and tear, such as vibration patterns or temperature changes, to predict when maintenance is needed.
- Analysing data from sensors or other sources, such as historical maintenance records, to identify patterns or trends that indicate when equipment is likely to fail.
- Using machine learning or other advanced analytics techniques to predict when equipment is likely to fail based on data from sensors or other sources.
- Automating maintenance tasks, such as scheduling maintenance or ordering replacement parts, based on the predictions made by the predictive maintenance system.
- Monitoring and tracking the condition of the equipment over time to detect any changes that could indicate a potential failure.
- Proactive approach instead of traditional reactive maintenance.
New Versus Old Aircrafts
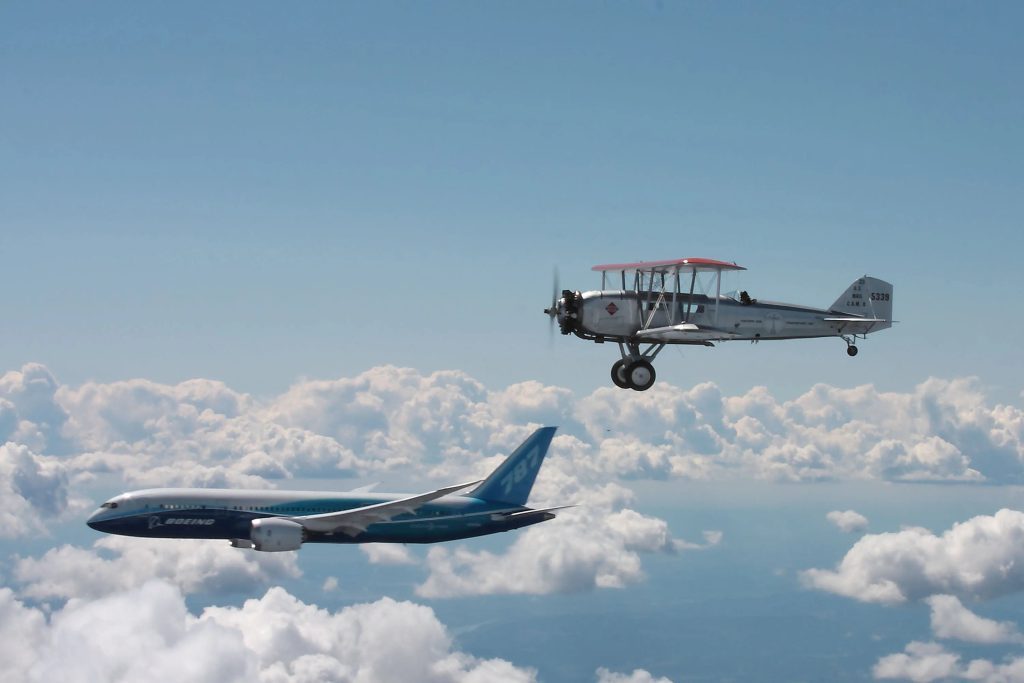
When we look at the advantages and disadvantages of using predictive maintenance on newer versus older aircraft, we see that the older aircraft types have the benefit of having more accumulated flight hours and maintenance experience, which can provide a large amount of historical data to develop and refine algorithms for predictive maintenance. However, newer aircraft types have the advantage of having more onboard sensors and better connectivity, which generates more data per flight. This data can be used to develop digital twins of systems and components, which can help predict their behaviour and possible failure during different flight phases.
Overall, both new and legacy aircraft can benefit from predictive maintenance, but in different ways. For example, legacy aircraft can benefit from the extensive maintenance experience and historical data, while newer aircraft can benefit from the comprehensive data generated by the onboard sensors and better connectivity.
Conclusion
In conclusion, predictive maintenance is a powerful strategy that can help organisations to improve equipment efficiency, reduce downtime, and prolong the life of their equipment. By monitoring equipment for signs of wear and tear, analysing data from sensors and other sources, and using machine learning and other advanced analytics techniques, organisations can predict when equipment is likely to fail and take preventative action to avoid unexpected failures. Predictive maintenance can be applied to both new and legacy equipment, but each has unique advantages and challenges. Nevertheless, organisations that invest in predictive maintenance can reap significant benefits, including cost savings and improved equipment performance. Furthermore, with the increasing use of IoT and advanced technologies like machine learning, the potential for predictive maintenance is only set to increase in the coming years. As such, organisations should consider implementing predictive maintenance as part of their overall maintenance strategy to stay competitive and improve their bottom line.
Complete list of Aircraft MRO + Cleaning Products under 1 Download
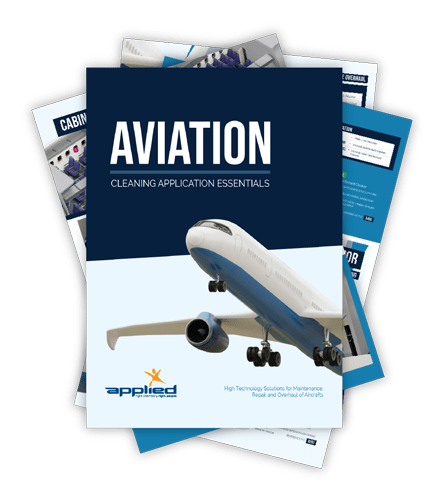