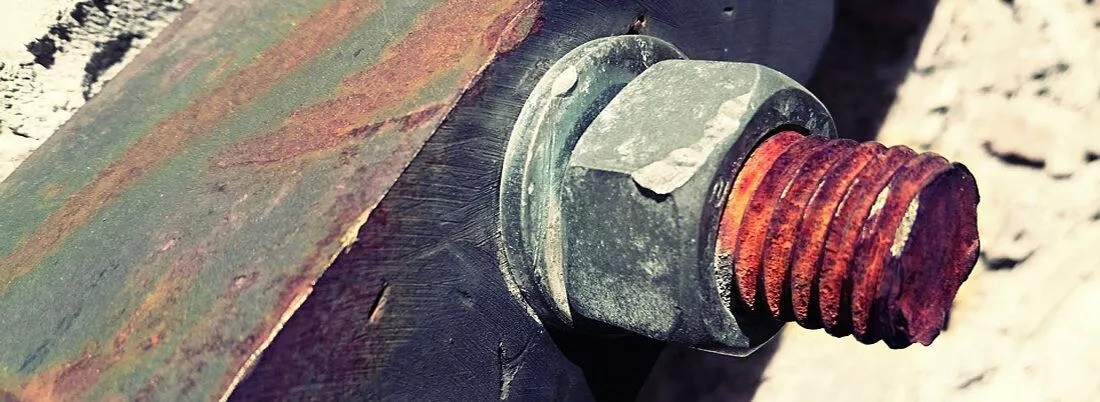
You may have been cautioned about using dissimilar metals, like carbon steel and stainless steel, in construction, and for good reason. This mistake has led to major disasters such as the Santa Barbara oil spill. However, it’s still possible to use these metals together if you do it the right way. We can help you understand galvanic corrosion and how to prevent it between carbon and stainless steel. Keep reading for a simple explanation.
Galvanic Corrosion in Stainless Steel
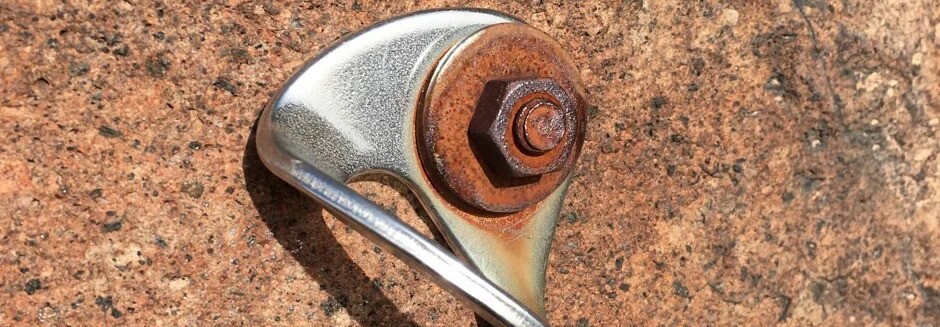
Stainless steel is known for its corrosion resistance due to the formation of a passive chromium oxide layer on its surface. However, it can still suffer from various types of corrosion under certain conditions, with galvanic corrosion being one of them.
Corrosion Resistance
Stainless steel is corrosion-resistant primarily because, when exposed to oxygen, it forms a passive chromium oxide layer on its surface. This layer acts as a barrier that prevents further oxidation and corrosion of the metal beneath.
Galvanic Corrosion
Factors Affecting Galvanic Corrosion
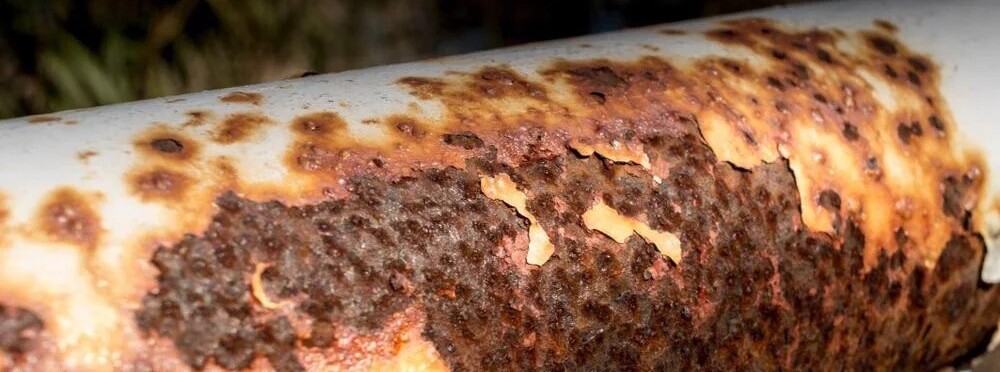
Electrochemical Potential Difference
The difference in the electrochemical potential between stainless steel and the other metal it’s in contact with is a primary driver for galvanic corrosion. Metals further apart in the galvanic series have a greater potential difference and, thus, a higher risk of galvanic corrosion.
Surface Area Ratio
The surface area ratio between metals in contact significantly affects galvanic corrosion rates, particularly in mixed-metal environments. When stainless steel, acting as the cathode due to its noble nature, has a larger surface area compared to a less noble metal acting as the anode (such as aluminium or carbon steel), corrosion of the anode accelerates. This disparity in surface area increases the cathodic efficiency, where more electrons flow from the anode to the cathode, promoting faster degradation of the smaller anodic surface. Engineers and designers must carefully consider and manage these surface area ratios through insulation, coatings, or physical separation of dissimilar metals to mitigate galvanic corrosion risks and preserve the longevity of structures and components in various environmental conditions.
Cathodic Protection
Cathodic protection involves using sacrificial anodes to protect a less noble metal by intentionally making it the anode within a galvanic cell. Sacrificial anodes, usually made of metals such as zinc or magnesium, are more reactive than the metal they safeguard (like steel or iron). When connected to the structure to be protected, sacrificial anodes corrode first, releasing electrons that flow to the less noble metal, thus preventing its corrosion. This method uses the sacrificial anode’s corrosion to protect the primary metal, effectively diverting corrosion processes away from critical components. Regular monitoring and replacement of sacrificial anodes are important to maintain effective cathodic protection systems in various industrial applications, including pipelines, ships, and offshore structures, where preventing corrosion is vital for longevity and structural integrity.
No Coatings
Coatings are applied to metals to prevent exposure to electrolytes and thus inhibit galvanic corrosion. These protective layers act as barriers that physically separate the metal surface from environmental factors like water or moisture. By covering either or both metals in a mixed-metal system, coatings effectively block the formation of a galvanic cell. For instance, applying a corrosion-resistant paint, polymer, or epoxy coating on the surface of both the stainless steel (cathode) and the less noble metal (anode) creates a barrier that prevents direct contact with electrolytes. This isolation reduces the likelihood of electron flow between the metals and minimizes the risk of accelerated corrosion. Coatings are widely used in various industries, including marine, automotive, and infrastructure, to prolong the lifespan of metal structures and components exposed to corrosive environments. Regular inspection and maintenance of coatings are necessary to ensure their integrity and effectiveness over time.
Environmental Control
Environmental control is crucial in mitigating galvanic corrosion by managing factors such as humidity, temperature, and exposure to corrosive chemicals. High humidity levels increase the conductivity of electrolytes, accelerating the corrosion process between dissimilar metals. By controlling humidity through ventilation or dehumidification systems, the moisture content in the air and on surfaces can be minimized, reducing the likelihood of galvanic corrosion. Additionally, controlling temperature can influence the rate of corrosion reactions; higher temperatures generally accelerate corrosion processes. Avoiding exposure to corrosive chemicals, such as acids or salts, also helps prevent the formation of aggressive electrolytes that can initiate or exacerbate galvanic corrosion. Implementing comprehensive environmental control strategies is essential in industries like marine, aerospace, and industrial manufacturing to preserve the integrity and functionality of metal structures and components over their operational lifetimes.
Difference Between Stainless Steel and Carbon Steel
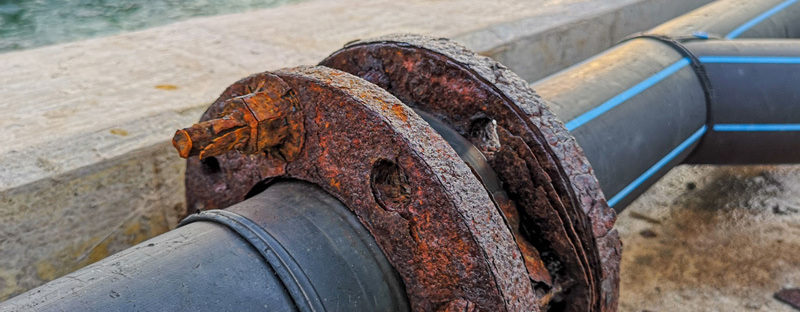
Not all steel is created equal. Some steels, like carbon steel and stainless steel, don’t mix well together. What sets these two common types of steel apart?
Carbon Steel
Stainless Steel
Stainless steel is resistant to corrosion because it contains chromium, which can resist corrosion when exposed to oxygen. When stainless steel and carbon steel are in contact and moisture is present, the stainless steel absorbs electrons from the carbon steel, causing the carbon steel to deteriorate rapidly.
Corrosion Prevention Between Stainless Steel and Carbon Steel
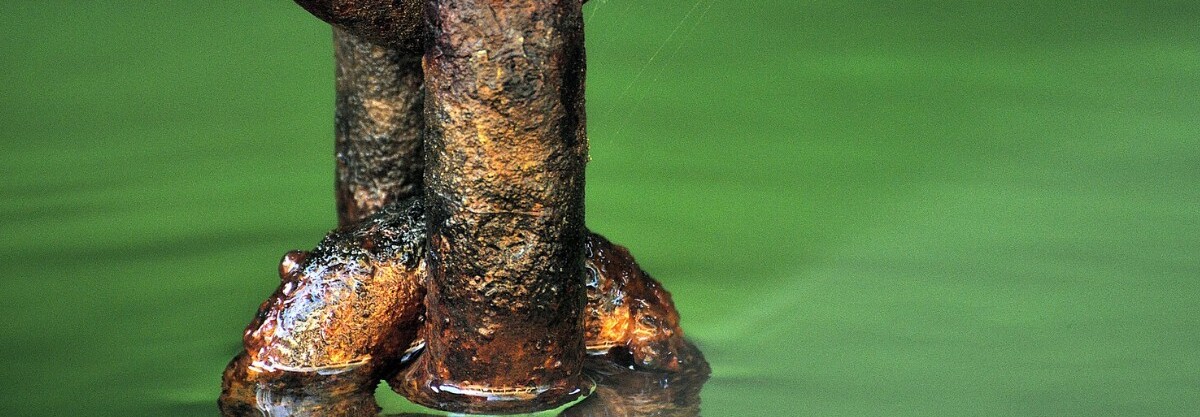
Use a Buffer
Plate the Carbon Steel
Reduce Exposure to Electrolytes
ORAPI RECOMMENDS:
PROTOR 842 is a water displacement type corrosion preventive designed for corrosion protection on
steel, brass and aluminum units or parts after machining, degreasing or cleaning.
Chemical Coating
To prevent corrosion, applying a chemical coating in joint areas where carbon steel overlaps with stainless steel, in addition to galvanizing can be effective. This coating creates a barrier that shields the metal surfaces from corrosive elements, reducing the likelihood of galvanic corrosion.
Conclusion
To prevent galvanic corrosion when using carbon steel and stainless steel together, it’s vital to understand factors such as electrochemical potential differences, surface area ratios, and environmental conditions. Effective strategies include using physical buffers, applying protective coatings, ensuring proper drainage, employing cathodic protection with sacrificial anodes, and regularly maintaining coatings to minimize corrosion risks and preserve the integrity and longevity of structures using dissimilar metals.
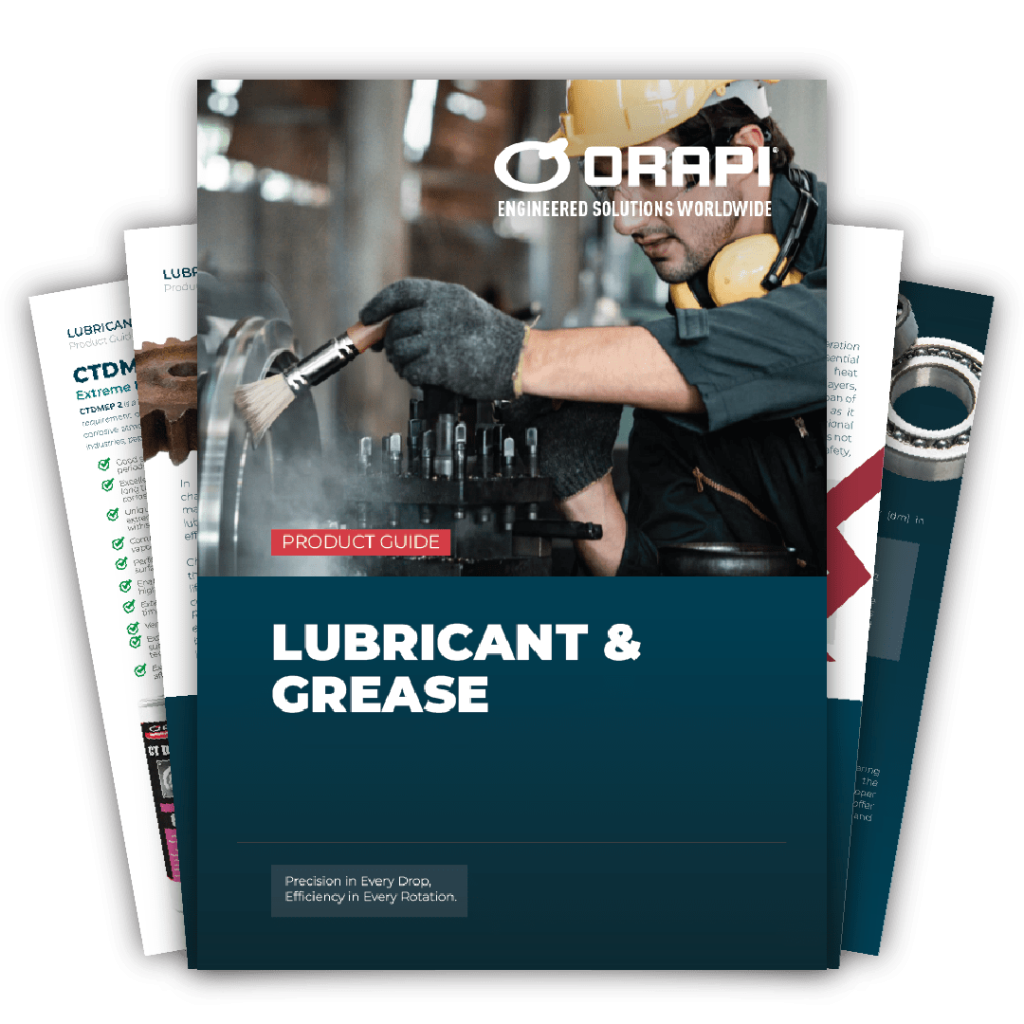