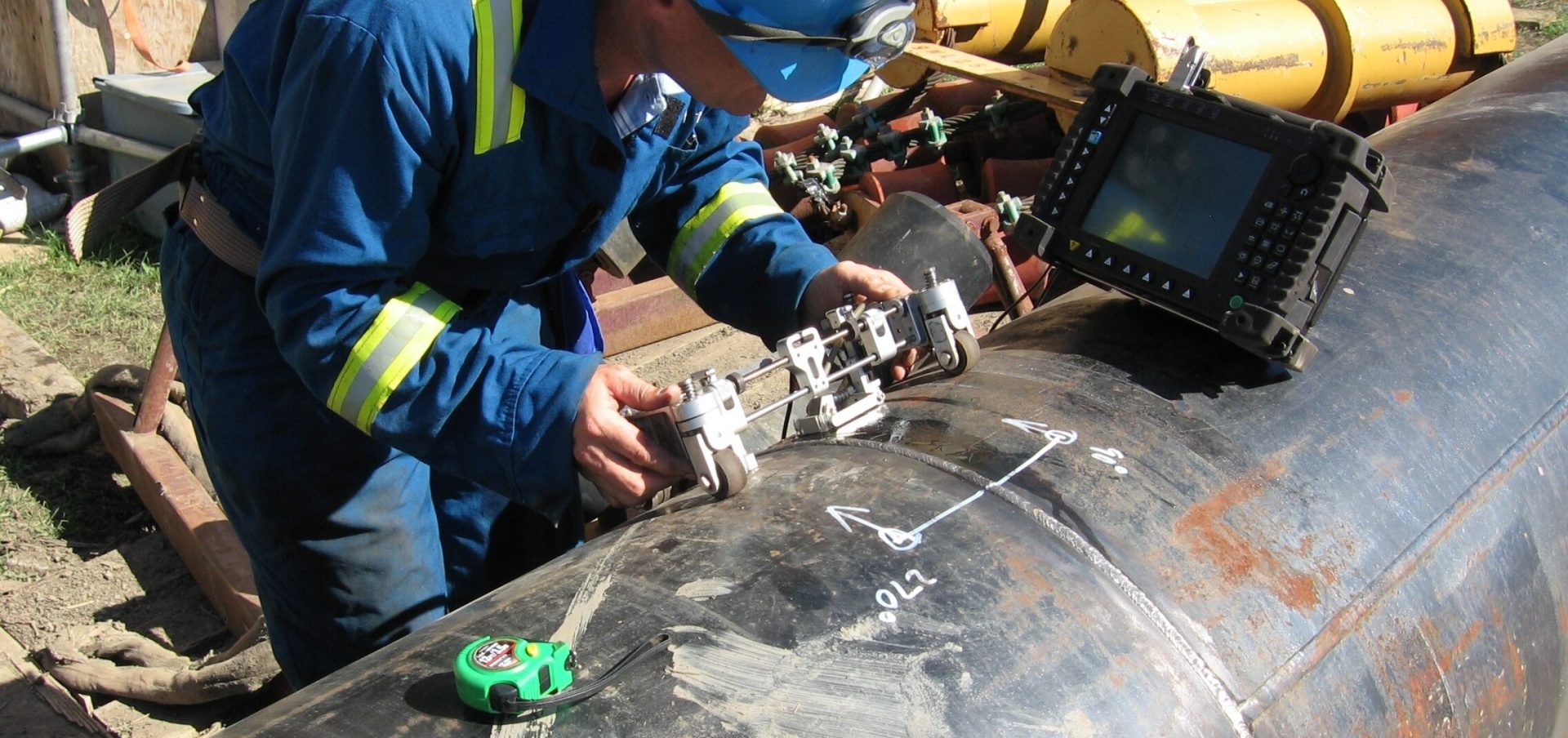
Corrosion is a process where metals degrade due to reactions with their environment, posing risks to industries such as oil and gas. Understanding this process is important for implementing effective corrosion monitoring technologies. These technologies enable early detection and prevention of corrosion and have seen recent advancements in accuracy and efficiency.
The Corrosion Process
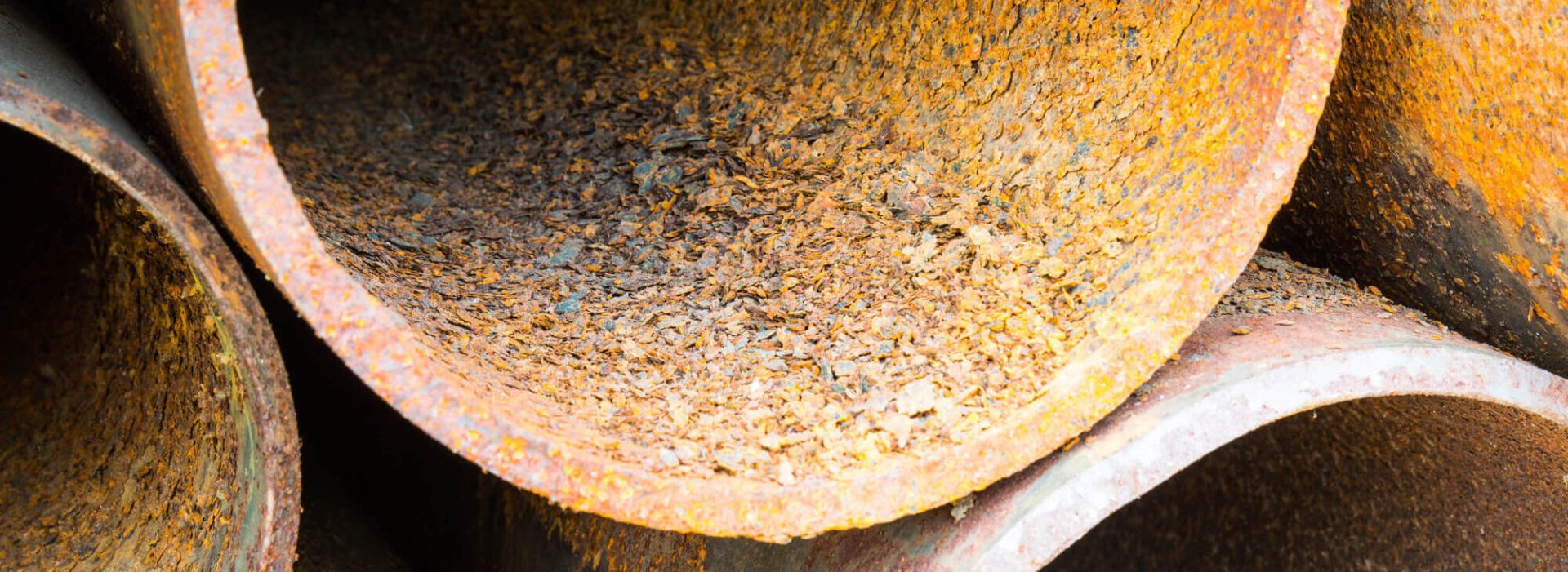
To effectively evaluate corrosion monitoring technologies, it is essential to understand what corrosion is and how it occurs. While various types of corrosion exist, this discussion focuses on the most common form in the oil and gas industry, where steel interacts with an aqueous environment and rusts.
The severity, speed, and effects of corrosion depend on multiple variables. Metallurgical factors include the composition, imperfections, internal stresses, and microstructure of the metal. Environmental factors encompass the pH level, temperature of the aqueous environment, and concentrations of water, oxygen, and various chemicals.
Corrosion is an electrochemical process where a metal reacts with its environment to form an oxide or another compound. This process involves three elements: an anode, a cathode, and an electrolyte. The anode is the site of the corroding metal, the electrolyte is the corrosive medium enabling electron transfer from the anode to the cathode, and the cathode forms the electrical conductor in the cell that is not consumed in the corrosion process.
When metal is exposed to a corrosive solution (the electrolyte), the metal atoms at the anode site lose electrons, which are then absorbed by other metal atoms at the cathode site. The cathode, in contact with the anode via the electrolyte, facilitates this exchange to balance its positive and negative charges. Positively charged ions are released into the electrolyte and are capable of bonding with other negatively charged atom groups.
The anodic reaction for iron and steel is:
Fe → Fe²⁺ + 2e⁻
Following the electron release at the anode site, four common cathode reactions can occur:
- Oxygen reduction in acidic solution:
- O₂ + 4H⁺ + 4e⁻ → 2H₂O
- Oxygen reduction in neutral or basic solution:
- ½O₂ + H₂O + 2e⁻ → 2OH⁻
- Hydrogen evolution from acidic solution:
- 2H⁺ + 2e⁻ → H₂
- Hydrogen evolution from neutral water:
- 2H₂O + 2e⁻ → H₂ + 2OH⁻
In the oil and gas industry, carbon dioxide (CO₂) and hydrogen sulfide (H₂S) are commonly present, with water acting as their catalyst for corrosion. When water combines with CO₂ and H₂S, the following reactions occur:
- H₂CO₃ Reaction:
- Fe + H₂CO₃ → FeCO₃ + H₂
- H₂S Reaction:
- Fe + H₂S + H₂O → FeS + 2H₂
These resulting molecules either attach themselves to the cathode or are released into the electrolyte, perpetuating the corrosion process. The production of hydrogen molecules is of particular concern to integrity managers, as it can significantly impact the structural integrity of the materials involved.
Corrosion Monitoring and Detection
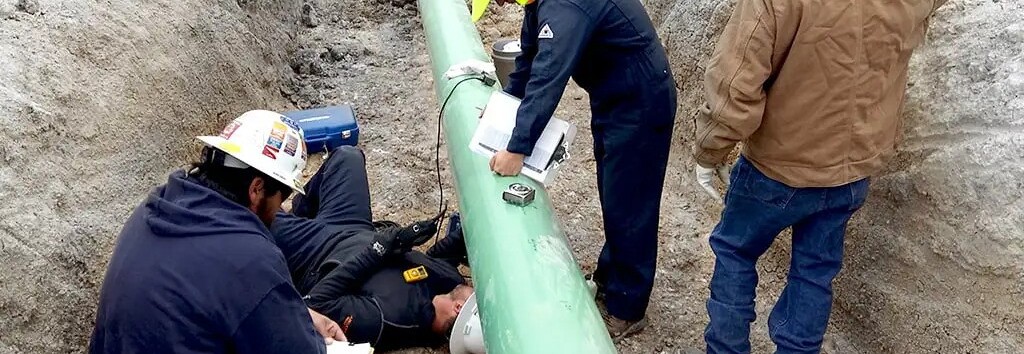
What is Corrosion Monitoring?
Corrosion monitoring involves assessing the corrosive nature of process stream conditions using probes inserted into the stream. These probes remain continuously exposed to the process stream and can take the form of mechanical, electrical, or electrochemical devices.
What is Corrosion Detection?
Recent Advancements in Corrosion Monitoring
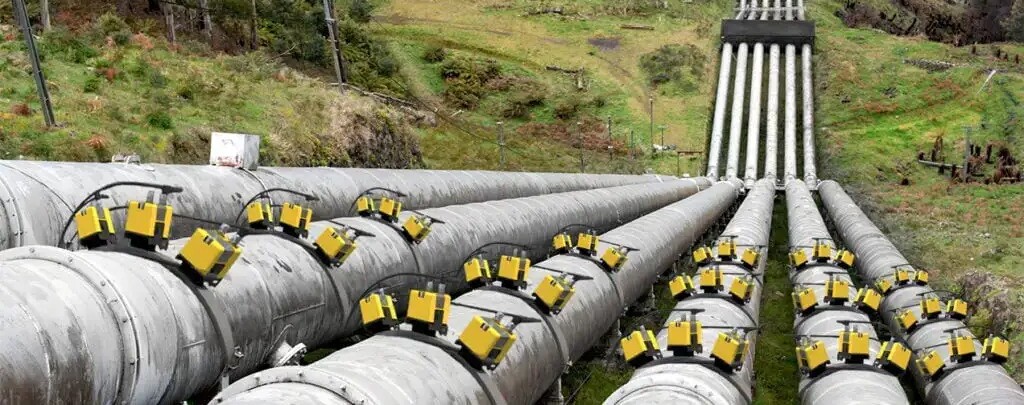
Corrosion monitoring has seen significant advancements, particularly in electrochemical techniques, non-destructive testing (NDT) methods, and remote monitoring systems. These innovations have improved corrosion detection accuracy, efficiency, and scope, enabling better maintenance strategies and asset management.
Electrochemical Techniques
Electrochemical Impedance Spectroscopy (EIS)
EIS is a powerful technique used to measure the impedance of a system, providing detailed insights into corrosion processes. It works by applying a small AC voltage to the metal surface and measuring the resulting current. The impedance, which varies with frequency, reveals information about the electrochemical properties of the metal-electrolyte interface. EIS can detect the formation of protective films, identify the initiation of corrosion, and assess the effectiveness of corrosion inhibitors. Its sensitivity to surface changes makes it a valuable tool for early detection and prevention of corrosion.
Linear Polarization Resistance (LPR)
LPR is another electrochemical method that measures the corrosion rate in real time. By applying a small perturbation to the potential of a corroding metal and measuring the resulting current, LPR determines the polarization resistance, which is inversely related to the corrosion rate. This technique provides quick and continuous corrosion monitoring, allowing for immediate response to changing conditions. LPR is particularly useful in environments where corrosion rates need to be closely watched, such as in pipelines and industrial systems.
If you’re seeking an evaluation of your facility’s processes by ORAPI to determine your eligibility for certification, you can access our assistance through the recently launched ORAPI Partner Program.
By signing up for the ORAPI Partner Program, you will enjoy many more benefits, such as having a dedicated account manager to assess, evaluate, and customise solutions; product and application training to make you aware of the protocols as well as educate your staff; and priority liaising with 24/7 agile support on-demand among many more.
Non-Destructive Testing (NDT) Methods
Advanced Ultrasonic Techniques
Ultrasonic testing has advanced significantly with the development of phased array ultrasonic testing (PAUT) and guided wave ultrasonic testing. PAUT uses multiple ultrasonic beams to create a detailed image of the internal structure of materials, allowing for precise detection of corrosion and other defects. Guided wave ultrasonic testing, on the other hand, employs low-frequency waves that can travel long distances along pipes and structures, making it ideal for inspecting inaccessible areas.
Ultrasonic Wall Thickness Sensors
Monitoring the wall thickness of pipes and vessels using continuous monitoring systems, such as permanently installed ultrasonic wall thickness sensors, provides real-time insights into corrosion, enabling more effective and proactive maintenance. These sensors transmit data wirelessly, allowing operators to continuously track metal loss due to corrosion, detect early signs of damage, and understand its impact. Real-time data facilitates timely interventions and risk mitigation, contrasting with periodic inspections that only offer a snapshot of the asset’s condition at specific intervals.
Eddy Current Testing
Eddy current testing has evolved to effectively detect corrosion under insulation (CUI) and other hidden areas. This method uses electromagnetic induction to produce eddy currents in the conductive material. Variations in the current flow indicate the presence of defects or corrosion. Advanced eddy current probes can penetrate insulation and detect corrosion without the need for removal.
Remote Monitoring Systems
Wireless Sensor Networks (WSNs)
WSNs have revolutionized corrosion monitoring by providing continuous, real-time data collection and transmission. These networks consist of numerous small, wireless sensors placed at various locations to monitor environmental conditions and corrosion rates. The sensors communicate with a central system, enabling remote monitoring and immediate alerts when critical thresholds are exceeded. WSNs are particularly advantageous in large-scale or hazardous environments where manual inspection is challenging.
Internet of Things (IoT)
The integration of IoT in corrosion monitoring has further enhanced the capabilities of remote systems. IoT devices can collect and analyze data from multiple sources, providing a comprehensive overview of corrosion conditions. This connectivity allows for predictive maintenance, as data analytics and machine learning algorithms can identify trends and predict future corrosion events.
Emerging Technologies
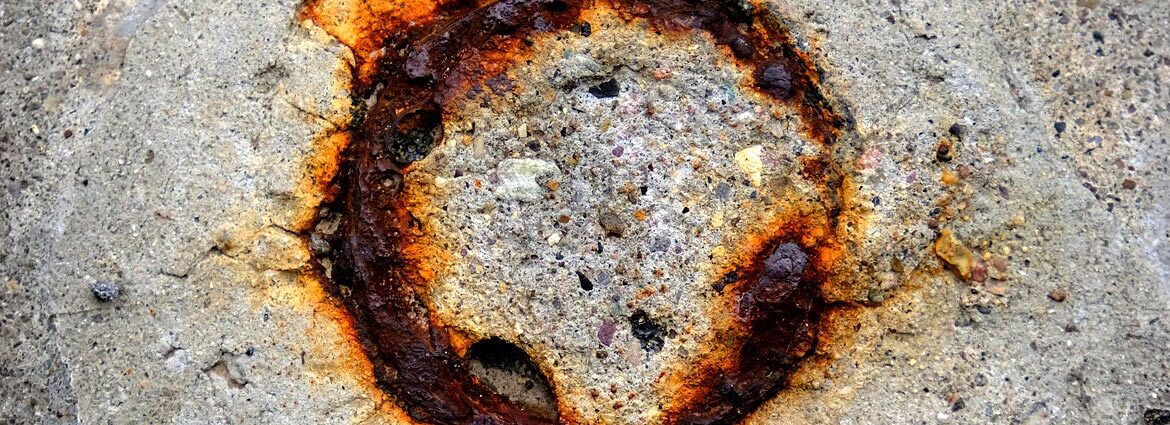
Fiber Optic Sensors
Fiber optic sensors have become a game-changer in corrosion detection due to their exceptional sensitivity and reliability. These sensors detect changes in strain and temperature related to corrosion by utilizing Fiber Bragg Gratings (FBGs), which alter the wavelength of light reflected within the fiber in response to environmental changes. This technology allows for precise monitoring of structural health in harsh and remote environments, such as deep-sea oil rigs and pipelines, providing real-time data without the interference of electrical signals.
Electromagnetic Acoustic Transducers (EMATs)
Electromagnetic Acoustic Transducers (EMATs) offer a significant advancement in non-destructive testing by eliminating the need for couplants, which are typically required in traditional ultrasonic testing. EMATs generate ultrasonic waves through electromagnetic induction, allowing them to inspect materials without direct contact. This makes them particularly effective for use in high-temperature or hazardous environments.
Machine Learning and AI
Machine learning (ML) and artificial intelligence (AI) are revolutionizing corrosion detection by enabling predictive maintenance and early detection of potential issues. These technologies analyze vast datasets from sensors and environmental conditions to predict corrosion rates and identify early signs of damage. AI systems continuously improve their accuracy, providing real-time insights that help optimize maintenance schedules and reduce costs.
3D Imaging and Laser Scanning
3D imaging and laser scanning technologies have transformed corrosion assessment by providing detailed and accurate visual representations of affected areas. Laser scanners emit beams that reflect off surfaces, creating precise 3D maps through time-of-flight or phase shift measurements. This technology is invaluable for inspecting large structures like bridges and industrial plants, capturing the extent and severity of corrosion with high precision. The detailed 3D models generated facilitate better decision-making for repairs and maintenance, allowing engineers to monitor corrosion progression and plan interventions.
Drones and Robotics
Drones and robotics have transformed corrosion inspection by accessing hard-to-reach areas and reducing human risk. Equipped with advanced sensors and cameras, drones capture high-resolution images and data around structures like bridges, offshore oil rigs, and industrial plants. Robotics, including crawlers and ROVs, navigate confined spaces and harsh environments, conducting detailed inspections without risking human safety. These technologies enable efficient assessments of structural integrity, identifying corrosion and defects that might be overlooked by conventional methods.
Benefits of Advanced Corrosion Monitoring
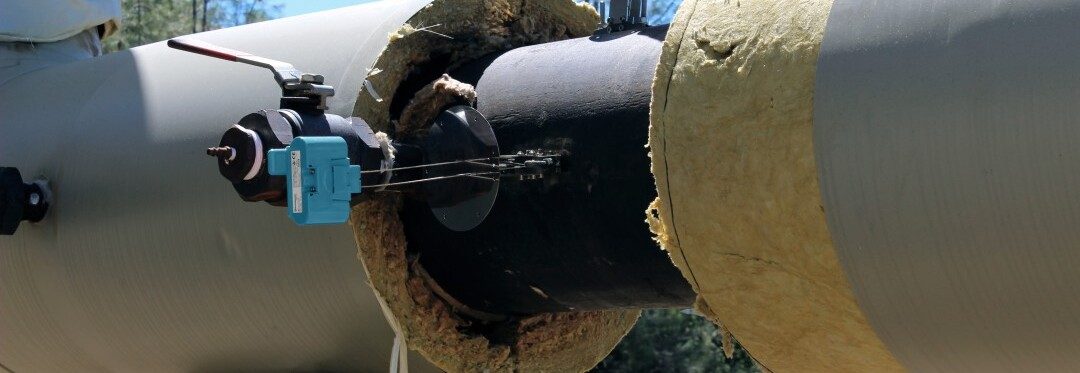
Increased Safety
Advanced corrosion monitoring technologies significantly enhance safety by providing early detection of corrosion, thereby reducing the risk of catastrophic failures in critical infrastructure such as bridges, pipelines, and industrial plants.
Cost Savings
Implementing advanced monitoring systems lowers maintenance costs and extends the life of assets by enabling predictive maintenance and timely interventions, preventing expensive repairs and downtime associated with unexpected failures.
Environmental Protection
By detecting and addressing corrosion early, advanced monitoring helps prevent leaks and spills that can cause significant environmental damage, safeguarding ecosystems and reducing the risk of costly environmental remediation.
Challenges and Future Directions
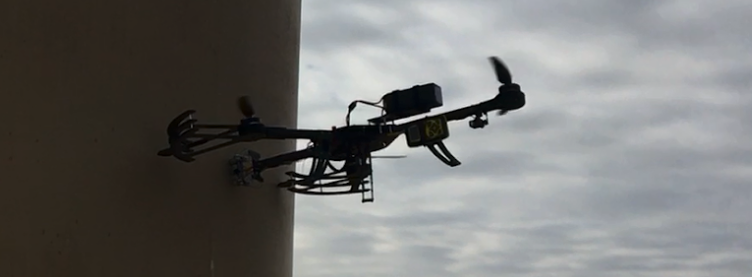
Technological Barriers
Despite the advancements, current corrosion monitoring technologies face limitations such as high costs, complexity, and the need for further miniaturization and integration. Research is needed to develop more cost-effective and user-friendly solutions.
Regulatory and Standardization Issues
There is a pressing need for standardized procedures and regulations to ensure consistent and reliable corrosion monitoring practices across industries. Establishing these standards will facilitate broader adoption and interoperability of advanced technologies.
Future Research
Ongoing research in nanotechnology, artificial intelligence, and advanced materials holds the potential for significant breakthroughs in corrosion detection and prevention. Innovations in these areas could lead to more accurate, efficient, and cost-effective monitoring solutions.
Conclusion
Effective corrosion monitoring is crucial for maintaining infrastructure in industries like oil and gas. Advances in electrochemical techniques, NDT methods, and remote monitoring systems have improved our ability to detect and mitigate corrosion, enhancing safety and reducing maintenance costs. This also contributes to environmental protection. As research develops more advanced solutions, the future of corrosion monitoring looks promising for better asset management and operational efficiency.