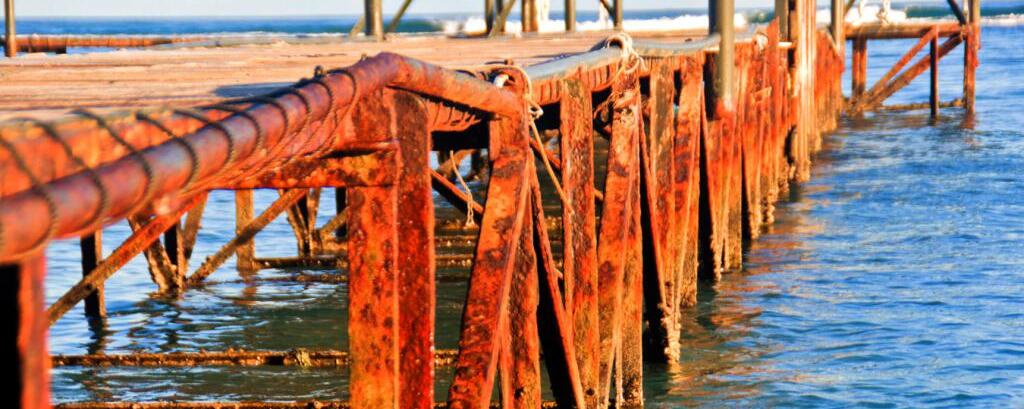
Marine corrosion is a complex phenomenon that involves both physical and chemical processes. It occurs when materials, especially metals, deteriorate due to their interaction with seawater and the marine environment. Factors contributing to marine corrosion include salinity, oxygen content, temperature, and biological activity. Marine corrosion can significantly affect marine structures, such as ships, offshore platforms, and pipelines, leading to structural integrity issues and increased maintenance costs.
Causes of Marine Corrosion
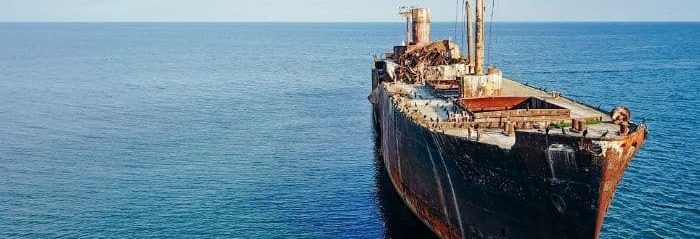
Marine corrosion is caused by physical and chemical/electrochemical factors. Physical corrosion, such as erosion and cavitation corrosion, occurs due to rapid liquid flow, the impact of sand on surfaces, and the high-speed rotation of the propeller. Additionally, higher concentrations of salts (e.g., NaCl, KCl, MgCl2, MgSO4, K2SO4), CO2, and O2 increase electrical conductivity and promote chemical corrosion. Microbiologically Influenced Corrosion (MIC) or biocorrosion occurs due to the presence or activity of microorganisms in biofilms on the metal surface, posing significant economic concerns.
Factors Leading to Marine Corrosion
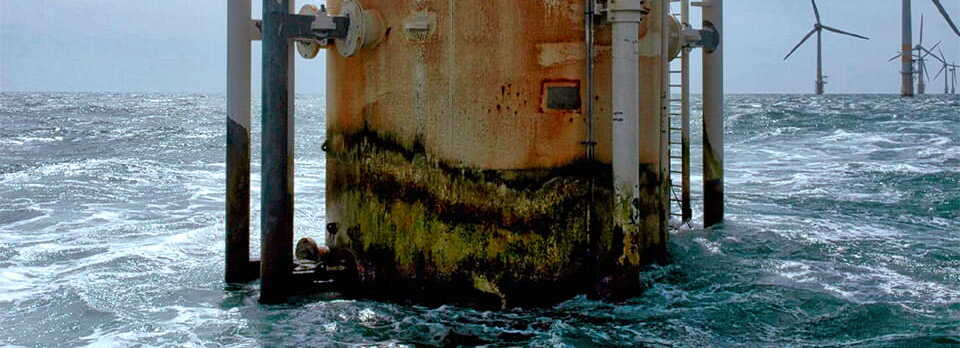
Salinity and Chloride Content
Salinity is the concentration of dissolved salts in seawater, mainly chloride ions. These ions disrupt the protective oxide layers that naturally form on metal surfaces, leading to corrosion. The high chloride content in seawater accelerates electrochemical reactions, degrading the material, thus making corrosion protection crucial for marine infrastructure such as ship hulls and offshore platforms.
Temperature and Humidity
Humidity, especially when combined with salty conditions, exacerbates corrosion. It creates a damp environment that sustains moisture containing electrolytes on metal surfaces, which enable electrochemical reactions and prevent the formation of oxide layers. In addition, fluctuating humidity levels can lead to cycles of condensation and evaporation, causing repeated wetting and drying of metal surfaces. This cycle intensifies corrosion, particularly in crevices and beneath coatings where moisture can accumulate.
Oxygen Levels and Biofouling
High oxygen levels accelerate the oxidation of metals, leading to uniform corrosion. Variations in oxygen concentration cause localized corrosion like pitting and crevice corrosion. Biofouling, the accumulation of microorganisms, algae, and small marine animals on submerged surfaces, exacerbates corrosion by forming biofilms that trap oxygen and moisture, altering local chemical environments. T These biofilms trap oxygen and moisture, leading to microenvironments with varying oxygen levels and pH, and produce corrosive by-products that directly attack metal surfaces.
Marine Microorganisms
Marine microorganisms significantly impact corrosion in marine environments through a process known as microbiologically influenced corrosion (MIC). Certain bacteria produce corrosive by-products, such as acids or sulfides, which directly attack the metal, while others can induce differential aeration conditions, enhancing electrochemical reactions. This can lead to accelerated material degradation, structural failures, and increased maintenance costs for marine infrastructure and vessels.
Types of Corrosion in Marine Environments

Uniform Corrosion
- Description: Uniform corrosion is characterized by a consistent and even removal of material across the entire exposed surface.
- Causes: This type of corrosion occurs due to the general exposure of metal surfaces to seawater and atmospheric conditions.
- Effects: Though often predictable, uniform corrosion can lead to significant material loss over time if not controlled.
Pitting Corrosion
- Description: Pitting corrosion is a localized form of corrosion that leads to the creation of small, often microscopic, pits or holes on the metal surface.
- Causes: It is typically caused by chloride ions in seawater that break down the protective oxide layer on metals like stainless steel.
- Effects: Pitting corrosion can lead to structural failure due to deep penetration, even if the overall material loss is minimal.
Crevice Corrosion
- Description: Crevice corrosion occurs in confined spaces where stagnant seawater or moisture can accumulate, such as under gaskets, bolts, and lap joints.
- Causes: The lack of oxygen in these crevices prevents the formation of protective oxide layers, leading to accelerated corrosion.
- Effects: This type of corrosion can be highly aggressive and often goes undetected until significant damage has occurred.
Galvanic Corrosion
- Description: Galvanic corrosion occurs when two different metals are electrically connected in the presence of an electrolyte, such as seawater.
- Causes: The more reactive (anodic) metal corrodes faster, while the less reactive (cathodic) metal is protected.
- Effects: Common in marine environments where different metals are used in construction, leading to rapid deterioration of the anodic material.
Stress Corrosion Cracking (SCC)
- Description: SCC is the growth of cracks in a corrosive environment, exacerbated by tensile stress.
- Causes: Factors include the presence of chlorides, high tensile stresses, and specific alloy susceptibility.
- Effects: This form of corrosion can lead to sudden and catastrophic failure of structures, even at stress levels below the material’s yield strength.
Intergranular Corrosion
- Description: Intergranular corrosion occurs along the grain boundaries of a metal.
- Causes: It is often due to impurities or depletion of alloying elements like chromium in stainless steel at the grain boundaries.
- Effects: This can weaken the material significantly, leading to loss of mechanical integrity.
Microbiologically Influenced Corrosion (MIC)
- Description: MIC is caused by the presence and activities of microorganisms, such as bacteria, algae, or fungi.
- Causes: Microorganisms can produce corrosive by-products like hydrogen sulfide or create differential oxygen concentration cells.
- Effects: MIC can lead to rapid and severe localized corrosion, often resulting in pitting and crevice corrosion.
Erosion Corrosion
- Description: Erosion corrosion is the accelerated deterioration of materials due to the combined effect of corrosion and mechanical wear.
- Causes: High-velocity seawater or abrasive particles can remove protective layers from metal surfaces, exposing fresh metal to corrosion.
- Effects: This type of corrosion is commonly found in marine piping systems, propellers, and other components exposed to fast-moving water.
Dealloying (Selective Leaching)
- Description: Dealloying involves the selective removal of one element from an alloy, leaving a weakened porous structure.
- Causes: Common in brass (dezincification) and other alloys, it is often driven by the electrochemical potential differences between the alloying elements.
- Effects: Dealloying can compromise the mechanical properties of the material, leading to brittle failure.
Different Materials’ Susceptibility to Corrosion
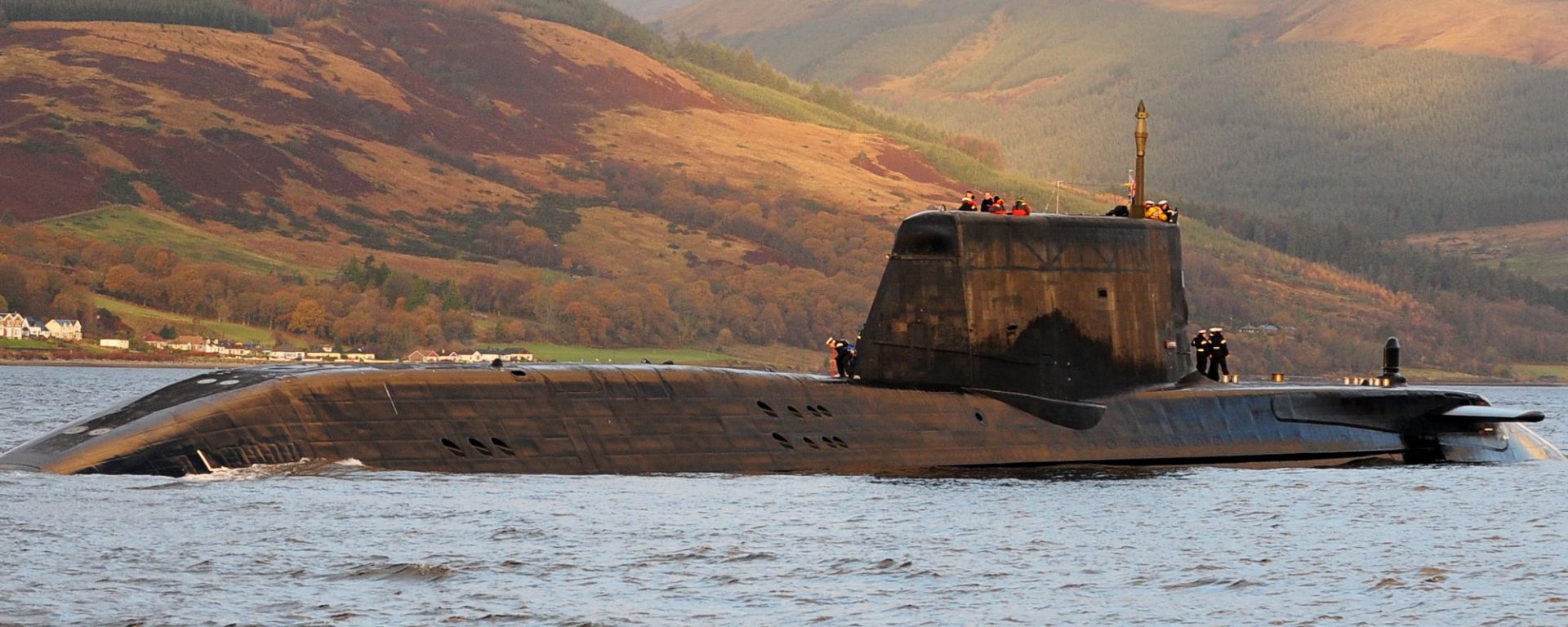
Dealloying (Selective Leaching)
Steel is widely used in marine environments but is prone to corrosion. Carbon steel corrodes due to electrochemical reactions with seawater, while stainless steel, which contains chromium, is more resistant due to the formation of a passive oxide layer. However, stainless steel can still suffer from corrosion in chloride-rich environments. Duplex stainless steel offers better resistance but is more expensive.
Aluminum and Its Alloys
Aluminum is often used in marine applications due to its lightweight nature and excellent resistance to corrosion. The protective oxide layer formed when exposed to air shields it from further oxidation, but can be compromised by chloride ions in marine environments, leading to pitting corrosion. Aluminum alloys, containing magnesium or silicon, offer better strength and corrosion resistance than pure aluminum, but can still be vulnerable to localized corrosion under harsh conditions.
Copper and Its Alloys
Copper and its alloys, including brass and bronze, are widely used in marine applications for their excellent resistance to biofouling and corrosion. Copper’s natural patina, a greenish layer that forms over time, provides a protective barrier against further corrosion. Brass, an alloy of copper and zinc, and bronze, an alloy of copper and tin, are particularly resistant to uniform corrosion and biofouling. However, these materials can suffer from dezincification (in the case of brass) and selective leaching, where specific elements are removed, weakening the alloy. Copper-nickel alloys are highly valued for their superior resistance to both corrosion and biofouling.
Non-Metallic Materials (e.g., Composites, Polymers)
Non-metallic materials like composites and polymers are increasingly used in marine environments due to their excellent corrosion resistance and lightweight properties. Composites, made by combining fibers (such as glass or carbon) with a resin matrix, are highly resistant to chemical and electrochemical attack. They are commonly used in boat hulls, offshore platforms, and underwater pipelines. Polymers such as PVC, HDPE, and epoxy coatings offer good resistance to seawater and can be used to protect metals or as structural materials. While non-metallic materials are generally immune to traditional forms of corrosion, they can degrade over time due to UV radiation, mechanical stress, or chemical exposure.
Effects of Marine Corrosion
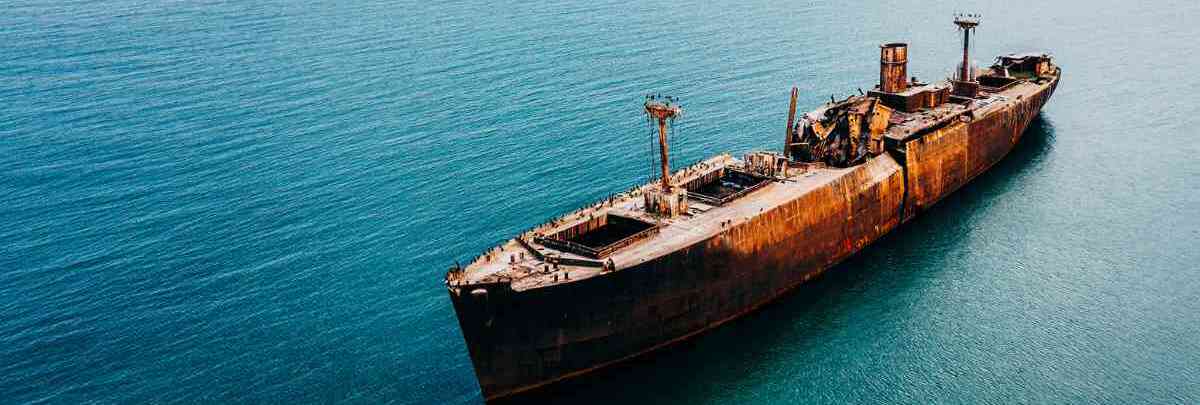
Structural Integrity and Safety Concerns
Corrosion weakens metal components by reducing their thickness and creating stress concentrations through pitting and cracking. This can lead to catastrophic failures in critical structures such as offshore platforms, bridges, ship hulls, and underwater pipelines. The safety of crew members, passengers, and marine operators is directly at risk when corrosion undermines the reliability of these structures, necessitating rigorous inspection, maintenance, and repair protocols to mitigate these hazards.
Economic Impact on Marine Industries
The economic impact of marine corrosion is profound, affecting various sectors of the marine industry, including shipping, oil and gas, fisheries, and coastal infrastructure. Costs include direct expenses for repair and maintenance, as well as indirect costs such as downtime and reduced operational efficiency. For instance, frequent ship repairs due to corrosion can cause operational disruptions and financial losses for shipping companies. In the oil and gas industry, corrosion-related failures can lead to costly shutdowns and loss of production. The financial burden on global industries is estimated to run into billions of dollars annually, prompting the need for advanced corrosion prevention strategies.
Environmental Consequences
Marine corrosion has significant environmental consequences, leading to the release of toxic substances such as heavy metals and chemicals into the marine ecosystem. Additionally, corrosion-induced failures in oil and gas infrastructure can lead to severe environmental pollution and damage to marine habitats. The need for frequent replacement and repair of corroded components also contributes to resource depletion and increased waste generation. Addressing the environmental impacts of marine corrosion requires stringent regulations, effective corrosion control measures, and the development of environmentally friendly materials and technologies.
How to Prevent Marine Corrosion
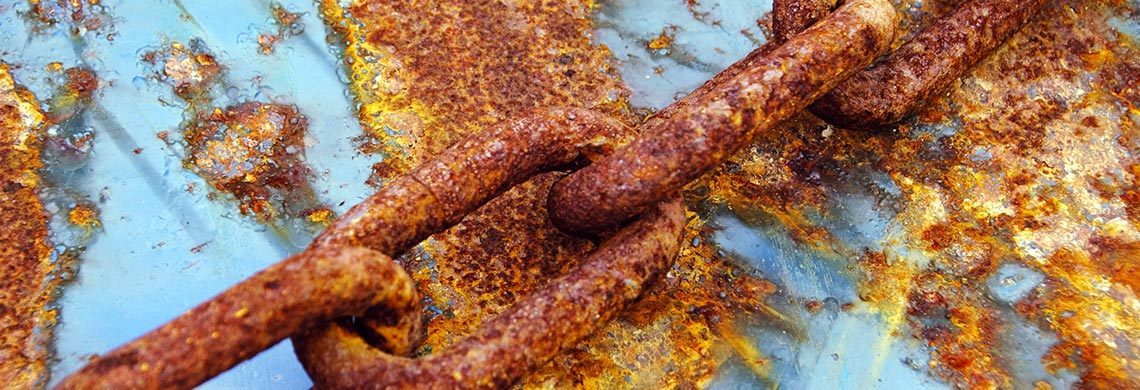
Coatings and Paintings
Anti-corrosive paints are specially formulated to create a resistant layer on metal surfaces, inhibiting corrosion. Epoxy coatings are durable and provide a tough protective barrier. Polyurethane coatings offer excellent UV resistance, ensuring prolonged protection. Bituminous coatings are commonly used for steel and concrete structures to protect against corrosive elements and extend lifespan. These coatings and paints extend the lifespan of marine structures and equipment by reducing the impact of corrosive processes.
ORAPI RECOMMENDS:
Cathodic Protection
Cathodic protection prevents marine corrosion by altering the electrochemical environment of the metal surface. One method is using sacrificial anodes, which attach more reactive metals like zinc, aluminium, or magnesium to the structure. These metals corrode preferentially, thereby protecting the primary metal from corrosion. Another technique is Impressed Current Cathodic Protection (ICCP), which uses an external power source to supply a continuous electric current. This current counteracts the natural electrochemical process that leads to corrosion.
Material Selection
Corrosion-resistant materials such as stainless steel, aluminum alloys, and titanium are inherently less prone to corrosion due to their chemical composition and protective oxide layers, making them ideal for marine applications. Additionally, composites and plastics are increasingly favoured for their excellent resistance to seawater corrosion, lightweight properties, and versatility. These materials do not rust and can withstand harsh marine environments without deteriorating, providing reliable and long-lasting solutions for various marine engineering needs.
Corrosion Inhibitors
Corrosion inhibitors interact with the metal surface in the marine environment to create a protective film, reducing the rate of metal degradation and enhancing durability. By altering the chemical environment, corrosion inhibitors reduce the rate at which metal components degrade. This method is particularly valuable for complex marine systems where physical protection methods like coatings may not be practical such as pipelines and engines. By using chemical additives strategically, the corrosive impact of seawater and other aggressive agents can be minimized, ensuring the integrity and functionality of marine structures and equipment.
ORAPI RECOMMENDS:
The fast-acting RUST OFF (formerly known as D-RUST) makes it possible to remove rust and oxidation more quickly, while special inhibitors reduce the impact on clean steel by 98%. RUST OFF is the speedy solution for removing rust from iron and steel.
Design Considerations
Effective design considerations are important in preventing marine corrosion by minimizing areas where corrosive processes can initiate and thrive. Avoid crevices in structural design because these small gaps can trap seawater, causing localized corrosion that is often more severe than general surface corrosion. By designing smooth and continuous surfaces and ensuring proper drainage, the risk of crevice corrosion is significantly reduced, helping to maintain the structural integrity and longevity of marine equipment and structures.
Environmental Control
Environmental control is a proactive approach to preventing marine corrosion by managing the conditions that facilitate corrosive processes. Dehumidification is a good strategy to reduce humidity levels in enclosed areas, thereby minimizing the moisture that can lead to corrosion. Sealing compartments is an effective measure to prevent water ingress and protect vulnerable parts of the structure from direct exposure to seawater and moisture. This method involves using seals, gaskets, and other barriers to create watertight compartments, ensuring that water cannot penetrate and cause damage. Together, dehumidification and sealing compartments help maintain a controlled environment.
Regular Maintenance and Inspections
Regular maintenance and inspections are important for managing and preventing marine corrosion. Routine cleaning and thorough inspections are needed to detect early signs of corrosion. Prompt touch-up repairs involving the reapplication of anti-corrosive paints or coatings help maintain the integrity of protective barriers. Consistent maintenance and proactive inspections extend the service life and safety of marine structures and vessels.
Conclusion
In conclusion, marine corrosion is a complex challenge with significant impacts on structural integrity, economics, and the environment. Advanced coatings, cathodic protection, and strategic design, along with regular maintenance, are key to mitigating these effects. Continued interdisciplinary collaboration and research are essential for developing and enhancing solutions for the sustainability and safety of marine operations.
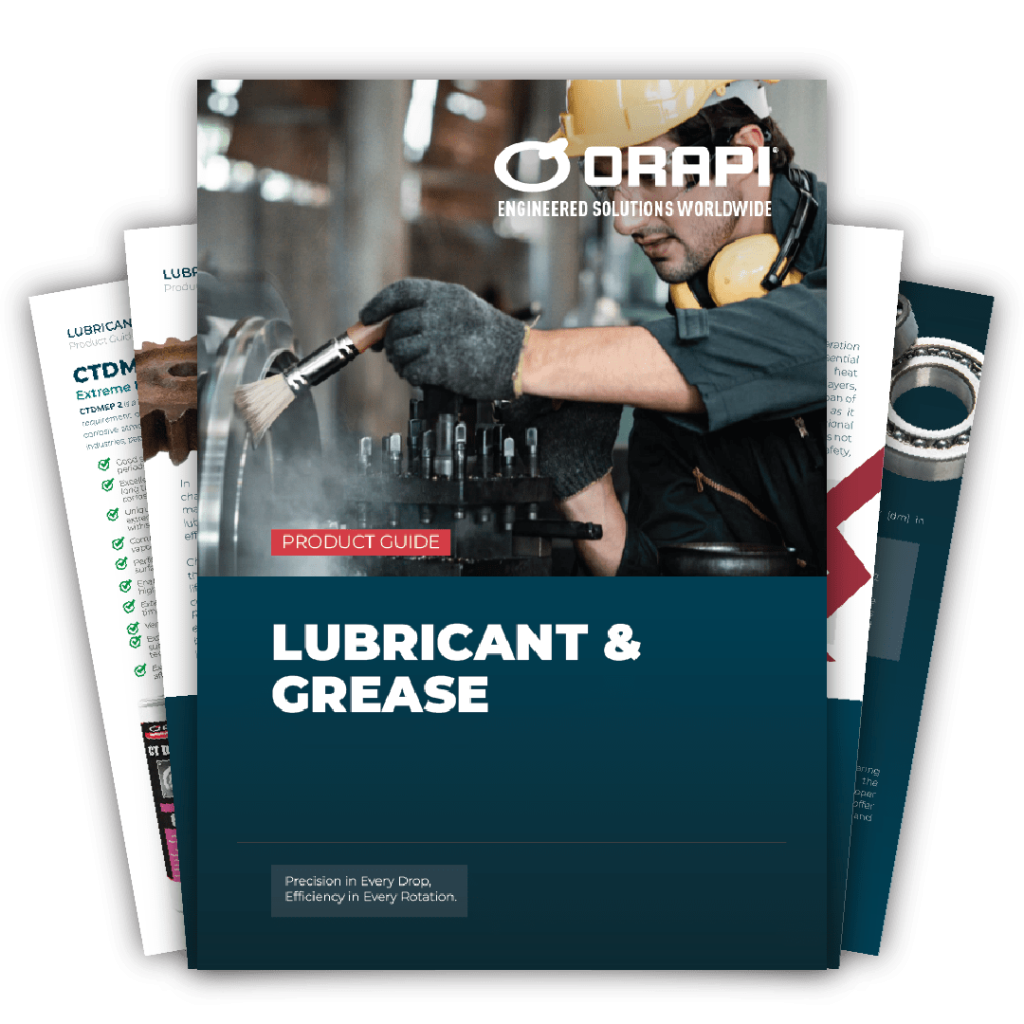