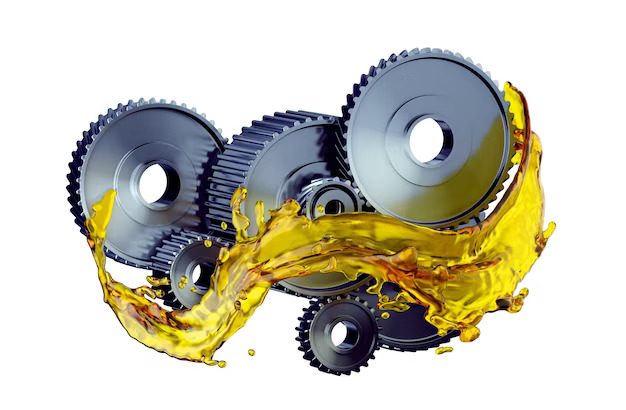
ORAPI RECOMMENDS:
Below we have mentioned some common types of lubricants and their applications:
Lubricating Oils
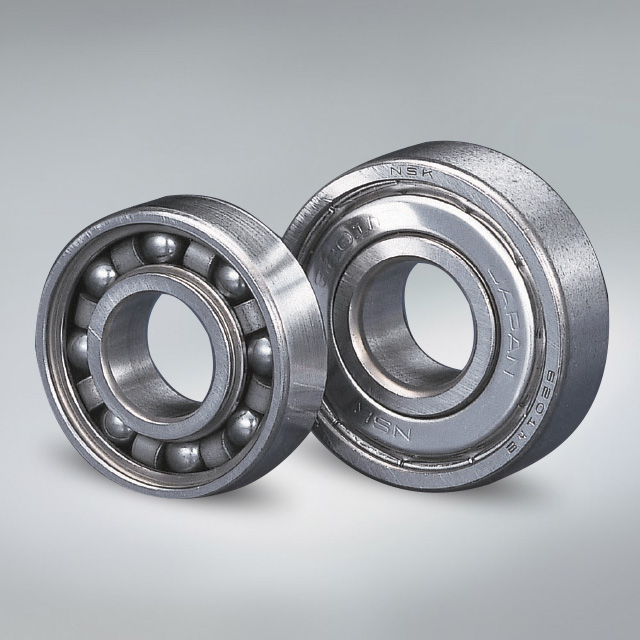
Benefits
Oils are an excellent choice for lubricating machinery and equipment in situations where the use of grease is not practical or desirable. Here are some benefits of using lubricating oils:
- Oils are versatile lubricants, and their applications include lubricating hinges, bearings, tools, and blade sharpening.
- Unlike grease, oils do not create significant resistance, making them ideal for applications requiring minimal friction.
- If you need to lubricate something difficult to reach or disassemble, oils can be wicked into tight spaces, providing adequate lubrication without disassembly.
When Not to Use
- Using oil lubricants is not suitable for machines or dirty or dusty parts, as adding oil to a compromised surface will increase friction and cause the oil to thicken. In addition, if the surface is not clean, oils with low viscosity may drip or run, making them ineffective for lubrication.
- Oil lubricants are not recommended in wet environments as they will be washed away. Although oil can repel water to some extent, it absorbs water over time, reducing its adhesion and causing the parts to be washed away. This is a common misconception that oil makes things waterproof.
ORAPI RECOMMENDS:
Grease Lubricants and Their Applications
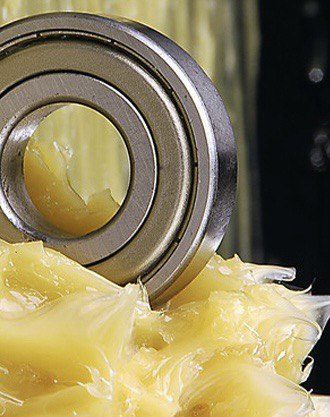
Benefits
Consider using grease if you’re looking for a reliable, long-lasting lubricant for your machinery. Its adhesive properties and ability to repel contaminants make it an excellent choice for many applications.
- Grease is an ideal lubricant for various machinery components, such as gears, bearings, chains, and linkages. This is because it provides superior adhesion to surfaces, ensuring long-lasting lubrication.
- In addition to its adhesive properties, grease is also effective at keeping out contaminants like dust and water droplets, which can cause damage to machinery over time. This makes it an excellent choice for machinery regularly exposed to harsh environmental conditions.
- It can provide long-lasting lubrication even in machines that are used infrequently. This is because it doesn’t evaporate or drip away like liquid lubricants, meaning you can apply it once and forget about it for an extended period.
When Not to Use
While grease can be an excellent lubricant in many situations, it may not always be the best choice for machinery with fast-moving or delicate components. Here are a few reasons why:
- Firstly, the thick consistency of grease can create too much resistance, which can slow down or impede the movement of fast-moving parts. This can lead to issues like overheating or premature wear and tear.
- Secondly, moving parts can fling grease around, making it challenging to keep the surrounding area clean. This can be a problem in cleanroom environments or applications where cleanliness is critical.
- Lastly, thick grease can be too much of a barrier in fine or fast-moving mechanisms, impeding the necessary movement of components—a lighter lubricant, such as a high-quality oil, maybe a better choice.
ORAPI RECOMMENDS:
Penetrating Lubricants and Their Applications
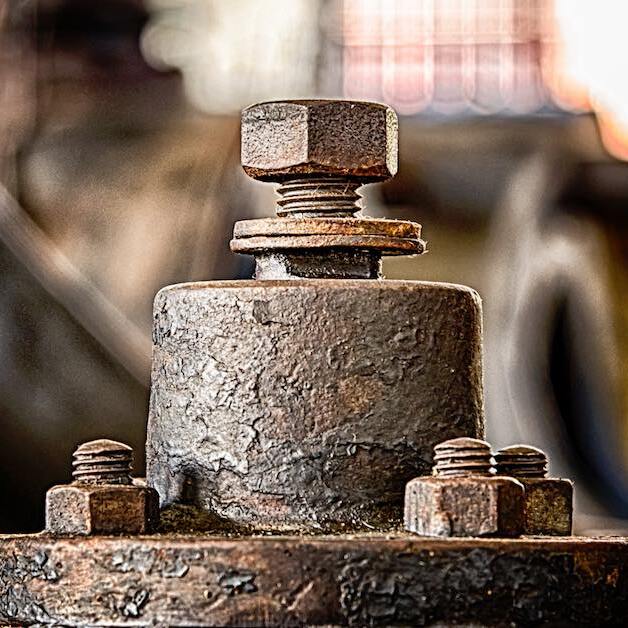
If you enjoy tinkering with engines or fixing things independently, you’ll appreciate the value of these special lubricants and their applications. Penetrating lubricants act as lifesavers for those tough-to-remove bolts and nuts. They’re not meant to provide long-lasting lubrication, but instead, they’re specifically formulated to seep into tight spaces, increase lubrication, and break down rust.
Benefits
Here are a few scenarios in which using a penetrating lubricant might be more appropriate than other types of lubricants:
- Penetrating lubricating oils are the go-to solution for freeing rusted or seized nuts and bolts. They can seep into the smallest crevices and dissolve rust and debris, causing obstruction.
- When dealing with stubborn adhesives, such as stickers or tape residue, penetrating oils can help break down the glue and make it easier to remove the adhesive.
- In warehouse repair tasks or other maintenance activities, penetrating oils can help break down buildup or corrosion on machinery or equipment.
When Not to Use
- Penetrating lubricants and their applications and benefits are unique, but it is vital to remember that they should not be used as a substitute for other lubricants.
- They should never be applied to bearings or other parts as they are short-lived and can cause damage to the machine. Therefore, it is essential to consider the specific application carefully and the intended use of a lubricant before deciding to use a penetrating lubricant.
ORAPI RECOMMENDS:
CB6 is a deeply penetrating, high-performance synthetic, and “clean” lubricant especially recommended to serve the critical demands of conveyors and chain drives systems working under severe loads, extreme temperatures and in a humid or dusty environment requiring maximum lubrication.
Dry Lubricants
Dry lubricants contain certain types of lubricants, such as silicon, molybdenum, graphite, and PTFE, that have a molecular structure that is extremely slippery and helps to reduce friction between surfaces. They can also be found in spray form, typically mixed with volatile solvents like alcohol or water and evaporates after application.
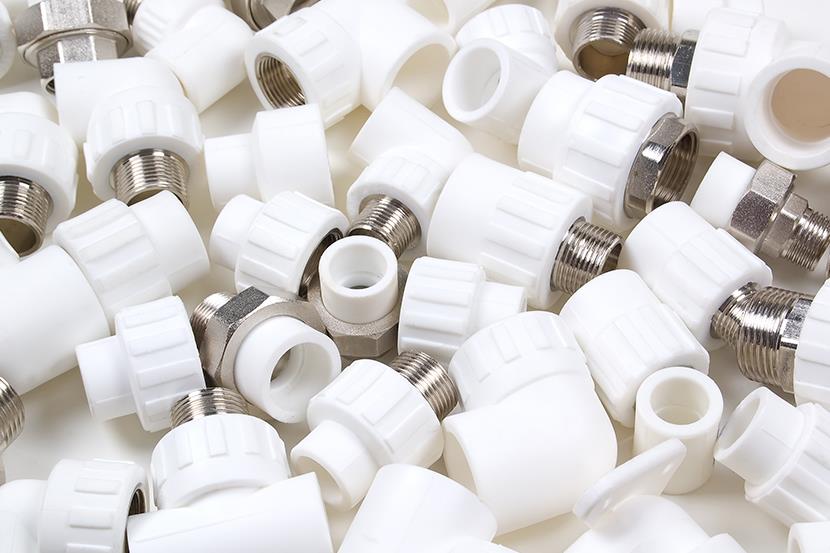
Benefits
Dry lubricants and their applications are recommended in the following situations:
- Dry lubricants are suitable for threaded rods, locks, and hinges.
- They are ideal for lubricating tiny parts that cannot be clogged with grease or surrounding surfaces that must be kept clean.
- Dry lubricants are an excellent choice to lubricate surfaces that do not attract dust or dirt.
- Dry lubricants are also practical when surfaces may be exposed to extremely high temperatures or pressures, as oils may start to oxidise under such conditions.
When Not to Use
- Avoid using dry lubricants in environments with high humidity or moisture levels, as the dry lubricant particles can absorb moisture and lose their effectiveness.
- Refrain from using dry lubricants in applications that require high loads or pressures, as they may not provide adequate lubrication in such situations.
- Avoid using dry lubricants on surfaces that require constant lubrication, as they may wear out quickly and require frequent reapplication.
- Do not expose the surface treated with dry lubricants to liquids or solvents, as any remaining lubricant may be washed away.
ORAPI RECOMMENDS:
Conclusion
In conclusion, it is crucial to understand the different types of lubricants and their applications to ensure that machinery and equipment operate at optimal levels. Lubricating oils are an excellent choice for various applications, while grease is ideal for machinery with slow-moving parts that require long-lasting lubrication. Penetrating lubricants are best suited for dislodging rust, debris, and other contaminants, and dry lubricants are ideal for applications where traditional lubricants cannot be used. Selecting the appropriate lubricant for each application can reduce machine downtime and failures and maximise productivity.
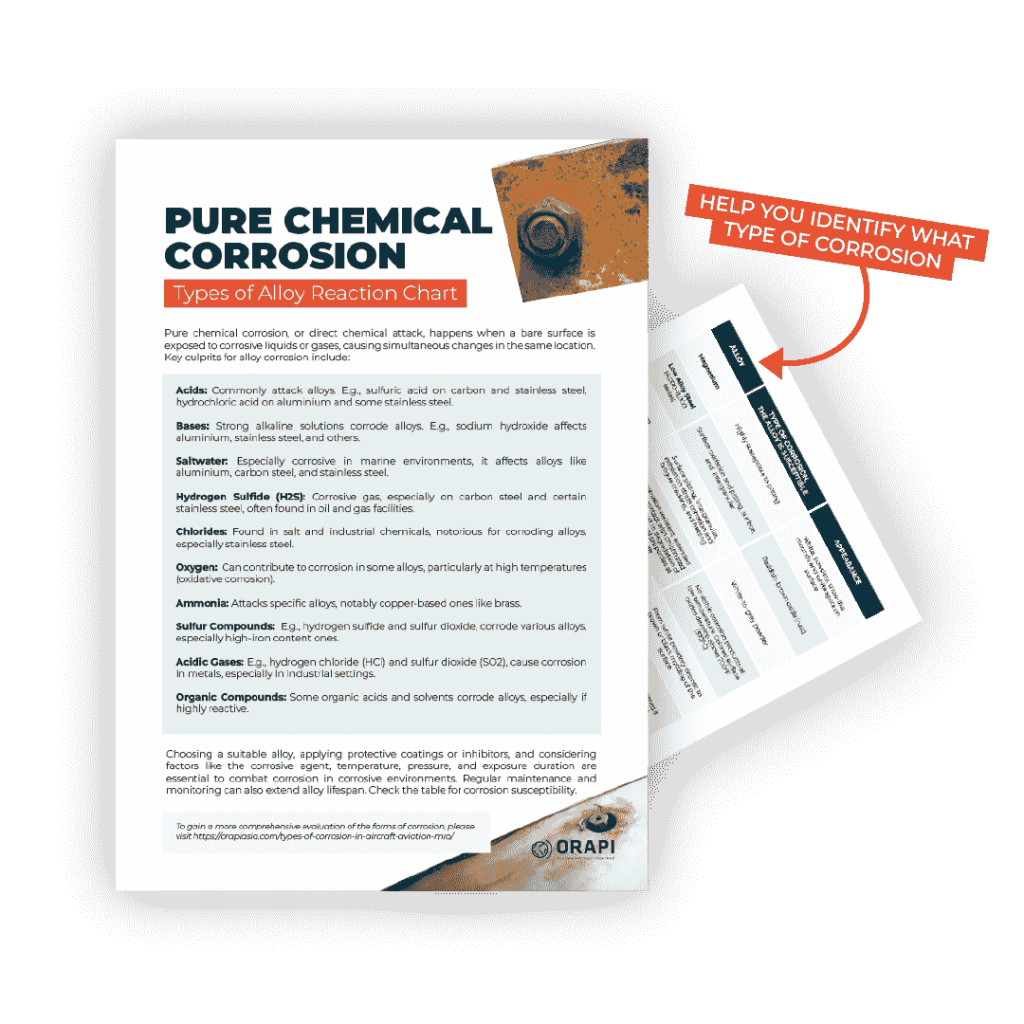