
Understanding Corrosion in Water Systems
Recognizing the different types of corrosion in water systems, understanding how and why they occur, and their impact on system metallurgy is important for developing a good water treatment program to control corrosion.
Once corrosion begins in a water system, it can rapidly escalate into a significant issue, leading to costly downtime, additional resource allocation, and financial losses for business owners. Globally, the costs associated with corrosion in water systems amount to billions of dollars annually. According to a study by NACE International, the global cost of corrosion across various industries, including water systems, is estimated to be around $2.5 trillion annually.
Corrosion in Water Systems

Corrosion-induced metal loss can significantly impact the reliability and lifespan of water systems and their components, including distribution pipes and related equipment. This degradation leads to higher maintenance costs and premature equipment failure. Additionally, corrosion can impair heat transfer efficiency, cause deposit buildup, restrict water flow, and ultimately reduce system efficiency. Proactively understanding and addressing the various types of corrosion and their causes can prevent them from escalating uncontrollably.
Types of Corrosion in Water Systems

Generalized Corrosion
This corrosion occurs uniformly across a metal surface, leading to widespread material loss. While generalized corrosion often causes fouling within a water system, it is less likely to result in sudden equipment failure.
Localized Corrosion
Localized corrosion manifests as small pits or depressions on the metal surface. This type is more problematic as it can lead to significant damage. Types of localized corrosion include pitting, under-deposit corrosion, galvanic corrosion, and microbiologically influenced corrosion (MIC) caused by organisms like Pseudomonas. Localized corrosion can create cracks or breaks in the metal, potentially leading to system failures.
What is Galvanic Corrosion?

Galvanic corrosion arises from a chemical reaction between two metals immersed in a conductive solution. This reaction essentially forms a basic battery, where one metal (the anode) corrodes while the other (the cathode) is protected.
The rate of galvanic corrosion depends on the specific metals involved. A galvanic potential chart can help predict the likelihood and rate of corrosion. To control galvanic corrosion, devices like dielectric unions are used to separate the metals. These unions break the electrical circuit, typically made from galvanized steel and lead-free brass, preventing electrolysis and subsequent corrosion.
What is Pitting Corrosion?

Pitting corrosion is a highly unpredictable and destructive form of metallic corrosion. It occurs when specific areas of a metal surface undergo intense, localized corrosion while the majority of the surface remains unaffected.
Several factors increase the risk of pitting corrosion, including stagnant water conditions and low water flow velocity. Corrosive ions, such as chlorides, sulfates, and oxygen, further exacerbate the risk. Once a pit forms as a depression in the metal surface, the trapped liquid within the pit becomes even more corrosive, accelerating the damage.
Under-Deposit Corrosion
Microbiologically Influenced Corrosion (MIC)

Erosion-Corrosion in Water Systems

What is Tuberculation?

Tips to Help Prevent Corrosion in Water Systems

Use a Water Softener
Water softeners can reduce the hardness of water by removing minerals such as calcium and magnesium, which are known to contribute to scale formation and corrosion. By softening the water, you minimize the deposition of these minerals on the surfaces of pipes and other components, thereby reducing the risk of corrosion.
Install a Corrosion Control System
Corrosion control systems involve the addition of chemicals or treatments to the water to inhibit corrosion processes. For example, inhibitors like phosphates can be added to form a protective film on the metal surfaces, while pH adjusters can balance the water chemistry to make it less corrosive. These systems are tailored to the specific needs of your water system to provide optimal protection.
Keep Your Water Temperature Low
Hot water accelerates chemical reactions, including corrosion. Keeping the water temperature as low as practical can significantly reduce the rate of corrosion. This is particularly important in systems where metals like copper and iron are present, as higher temperatures increase the solubility of oxygen and other corrosive agents, exacerbating corrosion.
Avoid Using Harsh Chemicals
Harsh chemicals such as bleach and certain acids can damage the protective oxide layers on metal surfaces, leading to increased corrosion. Instead, use milder cleaning agents that do not react aggressively with the metal components of your water system. Regular maintenance with appropriate cleaning agents can help preserve the integrity of the system.
ORAPI RECOMMENDS:
Have Your Water Tested Regularly
Regular water testing is crucial to monitor the quality of your water and detect any changes that could lead to corrosion. Tests can reveal high levels of acidity, alkalinity, chlorides, or other corrosive substances. Early detection allows timely intervention, such as adjusting the water chemistry or enhancing corrosion protection measures, to prevent extensive damage.
Conclusion
Understanding corrosion in water systems is important for effective prevention and maintenance. Proactive measures like water softening, corrosion control systems, regular water testing, and maintaining appropriate water temperatures can significantly reduce maintenance costs and extend equipment lifespan. These practices help businesses mitigate financial and operational risks associated with corrosion, ensuring the longevity and efficiency of their water systems.
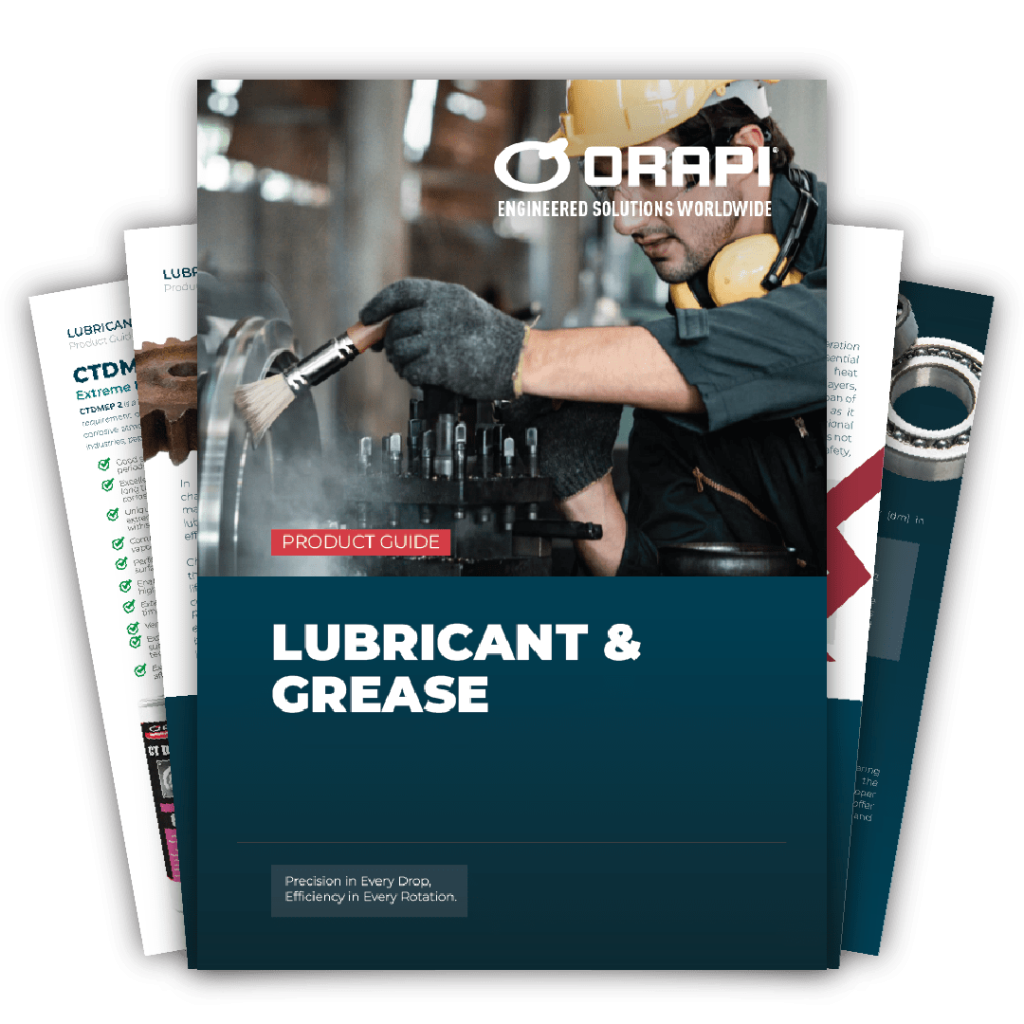