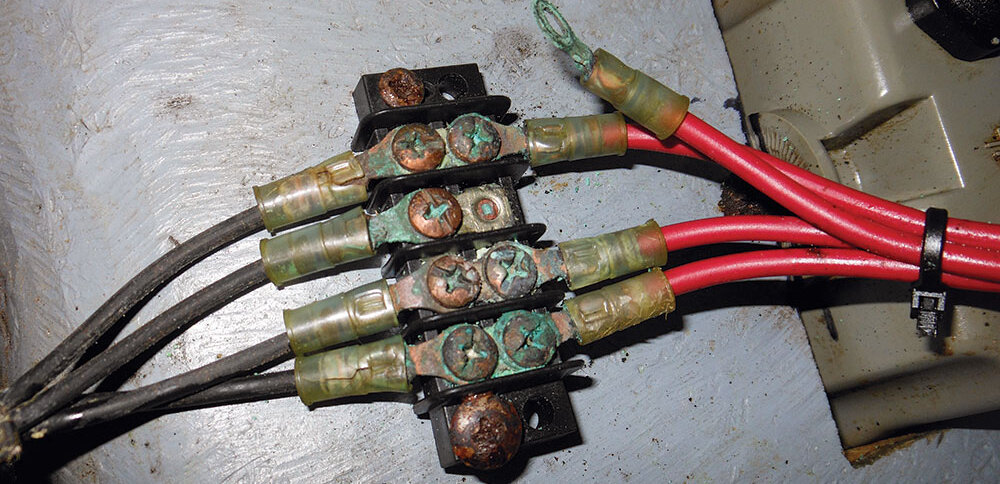
Corrosion in Electronics
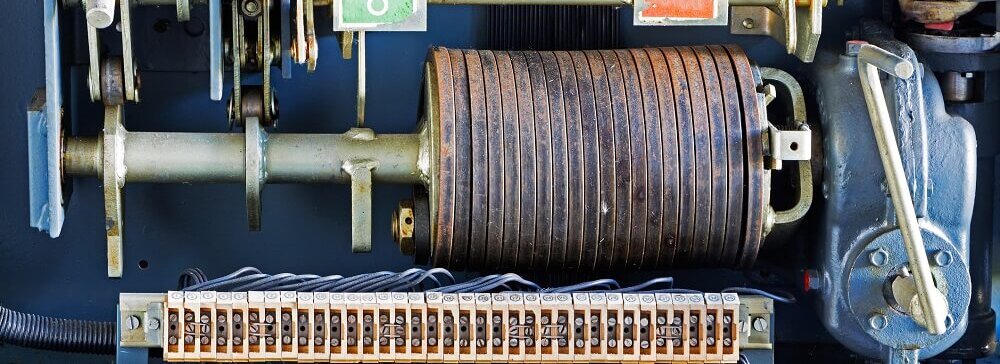
Corrosion is a significant issue in electronics due to the various materials used, each interacting differently in different environments. Electronics contain resistors, capacitors, inductors, integrated circuits, and printed circuit boards, which span a wide range of the periodic table, including various compounds and specific alloys. Different types of corrosion can affect these materials, making everything susceptible to corrosion. Gold, which is highly non-reactive, is often used as a plating material to protect other metals, especially in switches where the contact area is critical. Aluminium forms a protective oxide layer in normal air, but even well-known passivation techniques have failure points. When different metals come into contact with an electrolyte, they create a circuit that leads to galvanic corrosion, which requires measures like expensive impressed current systems to prevent.
Factors Contributing to Corrosion
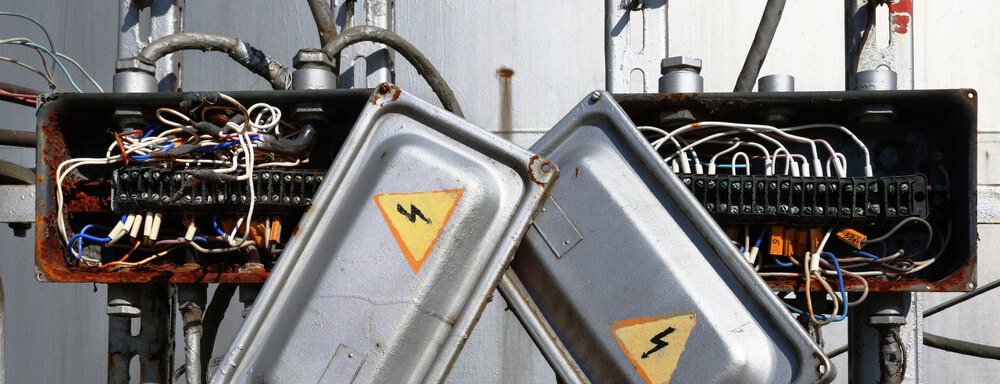
The primary factors contributing to corrosion in electronics are moisture, air composition, and temperature. Galvanic corrosion requires an electrolyte, meaning moisture must be present. Moisture can come from drops or spray of water or high relative humidity, which is hard to control, especially in storage and shipping. Air composition, including gases and ions, can significantly increase corrosion, with sulphur and nitrogen compounds and chloride ions being particularly problematic. Temperature increases the rates of all these reactions.
Electrochemical Reaction
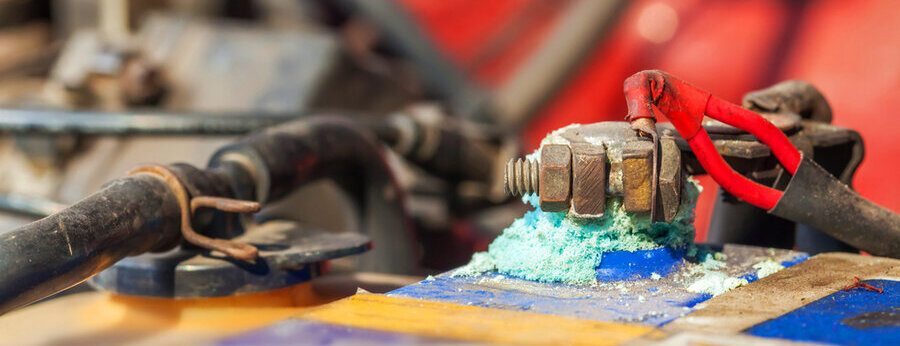
Corrosion in electronic components occurs due to electrochemical reactions, where metals in the electronic circuits interact with environmental factors, such as moisture and pollutants.
- Oxidation (Anodic Reaction): Metal in the electronic components loses electrons and forms positive ions.
- M→Mn++ne−
- Reduction (Cathodic Reaction): Electrons are gained by another species, often oxygen, in the presence of water.
- O2+4e−+2H2O→4OH−
Occurrence of Electronic Corrosion
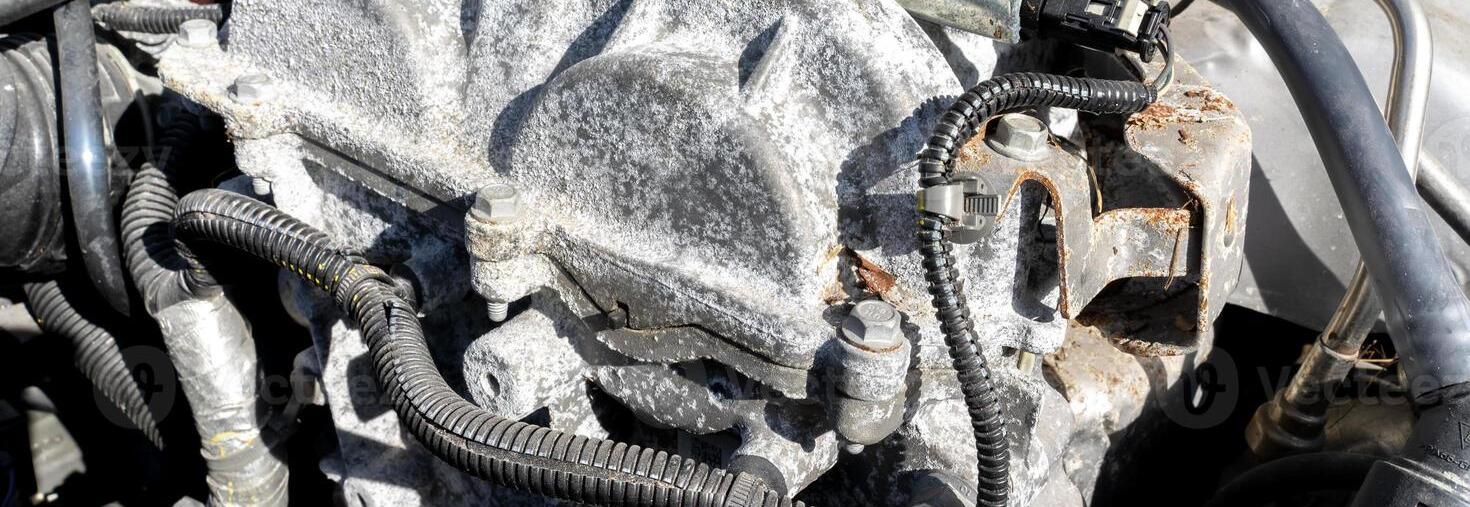
Electronic materials and devices corrode similarly to automobiles, bridges, and pipelines. However, their smaller dimensions make them significantly more susceptible to corrosion failure. Corrosion occurs when metals and conductive materials in electronic circuits undergo oxidation or other corrosive processes.
Electronic devices and components exposed to environments with moisture and corrosive gases such as SOx, NOx, H2S, and VOCs can experience corrosion on their metallic components. This corrosion can result in increased resistance, poor conductivity, short circuits, and, ultimately, the malfunction or failure of the affected electronic components.
Corrosion of metal components in electronic equipment can occur at various stages, including:
- Storage of components and assemblies
- Assembly
- Ship transportation
- Installation and service of electrical equipment
- Field operations of the equipment
Dendritic Corrosion
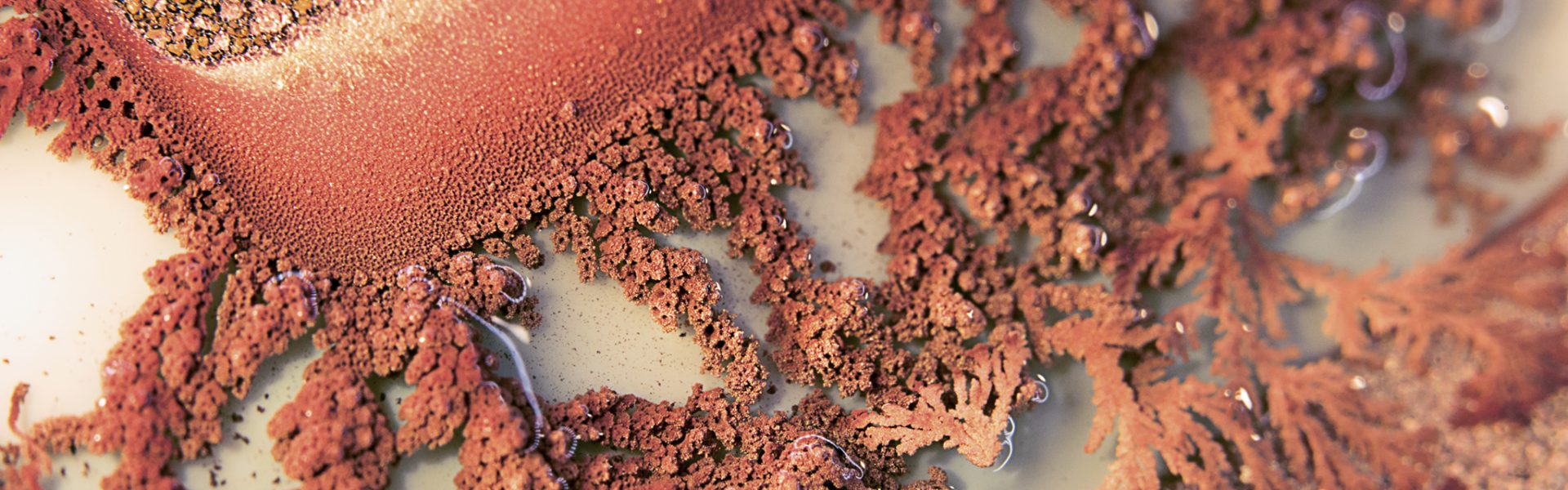
Damage or Loss of Electronics
As mentioned earlier, corrosion can severely damage electronics, causing them to weaken, malfunction, or fail completely. Since electronics are often expensive, this can result in a significant financial loss.
Damage or Loss of Metal Structures
While much of corrosion prevention focuses on electronics, it’s important to note that corrosion can also devastate metal surfaces and structures. Corrosion can cover these surfaces, weaken them, and even destroy them.
Maintenance, Repair, and Replacement Costs
Restoring damaged equipment is costly, as is purchasing new equipment to replace damaged items. If corrosion is widespread, these costs can quickly add up.
Additional Indirect Losses
Corrosion can lead to various risks. Fires may occur from unstable electronics, leaks may develop from unsealed pipes, and workers might get injured, leading to expenses from workers’ compensation and paid injury leave. There is even the potential for lawsuits if injuries occur. All these consequences can result from unchecked corrosion in your facilities.
Causes of Electronic Corrosion
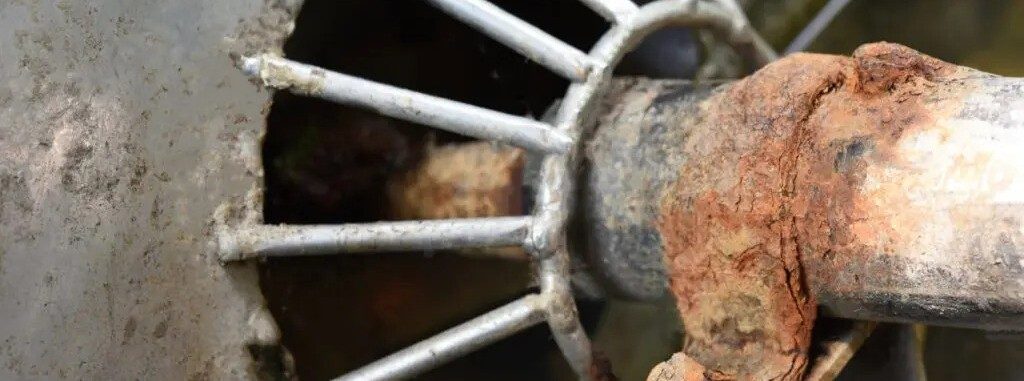
Conditions Facilitating Electrochemical Reaction
Presence of Electrolytes
Moisture often contains dissolved salts and pollutants, such as chloride ions from salt or sulphur compounds from industrial emissions. These substances enhance moisture conductivity, promoting electron flow between metal surfaces and accelerating the corrosion process, which leads to the degradation of metal components in electronic devices.
Electrical Potential Difference
When two metals with different electrochemical potentials are in contact with an electrolyte, they form a galvanic cell. In this cell, the metal with the lower potential acts as the anode and corrodes, while the metal with the higher potential acts as the cathode and is protected. This process accelerates the corrosion of the anodic metal.
Mechanical Stress
Mechanical stress and vibrations can significantly increase the susceptibility of metals to corrosion by creating micro-cracks or deformations on their surfaces. These imperfections serve as sites where corrosive agents, such as moisture and pollutants, can accumulate and penetrate deeper into the metal. The presence of these micro-cracks also increases the surface area exposed to the environment, thereby accelerating the corrosion process.
Environmental Factors Causing Electronic Corrosion
Moisture and Humidity
Exposure to moisture, such as rain, condensation, or high humidity levels, accelerates electronic corrosion. Water acts as a catalyst, promoting chemical reactions that lead to the oxidation of metals and the corrosion of electronic components.
Corrosive Gases
The presence of corrosive gases, such as sulphur oxides (SOx), chlorine (Cl2), and hydrogen sulphide (H2S), contributes to electronic corrosion. These gases react with metals, forming corrosive compounds that degrade electronic components over time.
Airborne Contaminants
Dust, dirt, and airborne particles exacerbate electronic corrosion. Contaminants can contain corrosive substances or provide a medium for moisture retention, accelerating the corrosion process.
Poor Storage Conditions
Inadequate storage, such as keeping electronics in damp or corrosive environments, can accelerate corrosion. Improper storage may expose microelectronic equipment, devices, or components to moisture or other corrosive elements, causing damage over time.
Areas and Activities Producing Electronic Corrosion Agents
Coastal Area
Electronics near coastal regions are at a higher risk of corrosion due to high humidity. Winds blowing from the sea bring moisture, leading to accelerated corrosion.
Industrial Facilities
Many industrial processes involve chemicals or high temperatures that produce corrosive gases. Metal refining, chemical manufacturing, and power plant combustion can release gases like sulphur dioxide (SO2), hydrogen sulphide (H2S), and nitrogen oxides (NOx). Processes such as welding, soldering, and cutting metals produce gases like ozone (O3), nitrogen dioxide (NO2), and chlorine (Cl2), which are corrosive to metals and other materials.
Automotive Vehicles
Vehicles powered by internal combustion engines emit corrosive gases as byproducts of fuel combustion, including sulphur oxides (SOx), nitrogen oxides (NOx), carbon monoxide (CO), and volatile organic compounds (VOCs).
Landfill Sites and Sewage Drains
These areas release corrosive gases, such as hydrogen sulphide and volatile organic compounds (VOCs), which react with moisture in the air to form corrosive compounds.
Agricultural Activities
Agricultural practices involving fertilisers, pesticides, and livestock farming generate corrosive gases. Ammonia (NH3) released from animal waste and nitrogen-based fertilisers can corrode nearby structures and equipment. Electronic devices and components exposed to outdoor environments are particularly susceptible to corrosion.
How to Prevent Electrical Corrosion
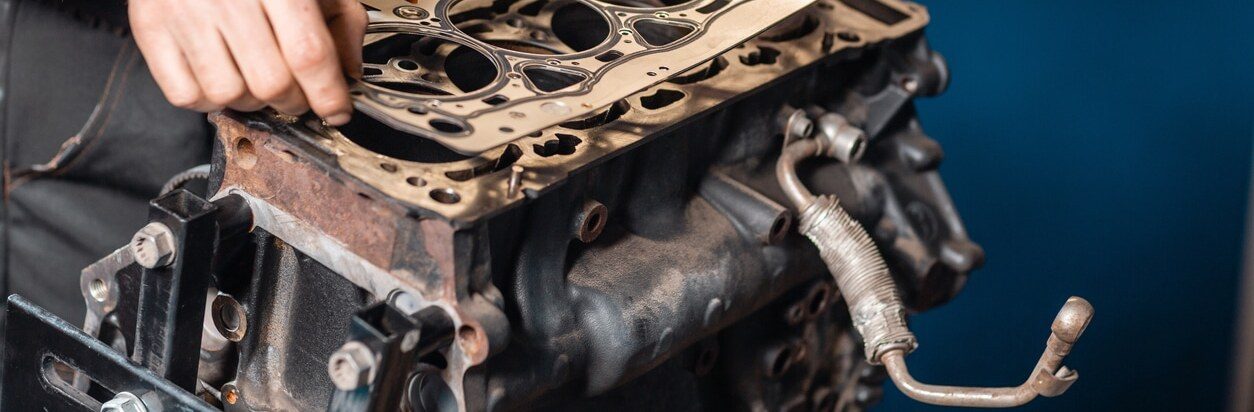
Protective Coatings and Materials
Applying corrosion-resistant coatings like conformal coatings or epoxy resins to electrical components prevents moisture and corrosive substances from reaching metal surfaces. These coatings act as protective barriers, ensuring that the underlying metals remain insulated from environmental factors that can cause deterioration. Selecting inherently resistant materials like stainless steel, aluminum alloys, or gold plating further enhances the durability and longevity of electrical components, especially in high-risk areas with unavoidable exposure to harsh conditions.
ORAPI RECOMMENDS:
Sealing and Enclosures
Using sealed enclosures is imoortant to protect electrical components from moisture and contaminants. High-quality gaskets and seals in junction boxes and connectors are essential to prevent damage to the electrical systems. Regular maintenance of these enclosures is fundamental in preventing electrical corrosion and maintaining system reliability.
Regular Maintenance and Inspection
Regular inspections of electrical systems are essential to detect corrosion early. Look for discoloration, rust, or other signs of corrosion on metal surfaces. Clean electrical components regularly to remove dust, dirt, or corrosive residues using appropriate cleaning agents that won’t damage the components.
Temperature Control
You can prevent corrosion in electrical components by maintaining optimal temperatures. Implement cooling systems to reduce the rate of corrosion and ensure the longevity and reliability of the electrical systems. By keeping the temperature within a safe range, these systems not only prevent thermal damage but also mitigate the risk of accelerated corrosion, enhancing the overall performance of the electrical components.
Conclusion
Electronic corrosion is a significant threat to electronic devices across industries. It results from electrochemical reactions due to factors like moisture and corrosive gases. This corrosion leads to higher maintenance costs, decreased productivity, and safety risks, especially in critical fields. Implementing preventive measures such as protective coatings, sealing, regular maintenance, and temperature control is essential to mitigate the effects of electronic corrosion and ensure optimal performance and safety.
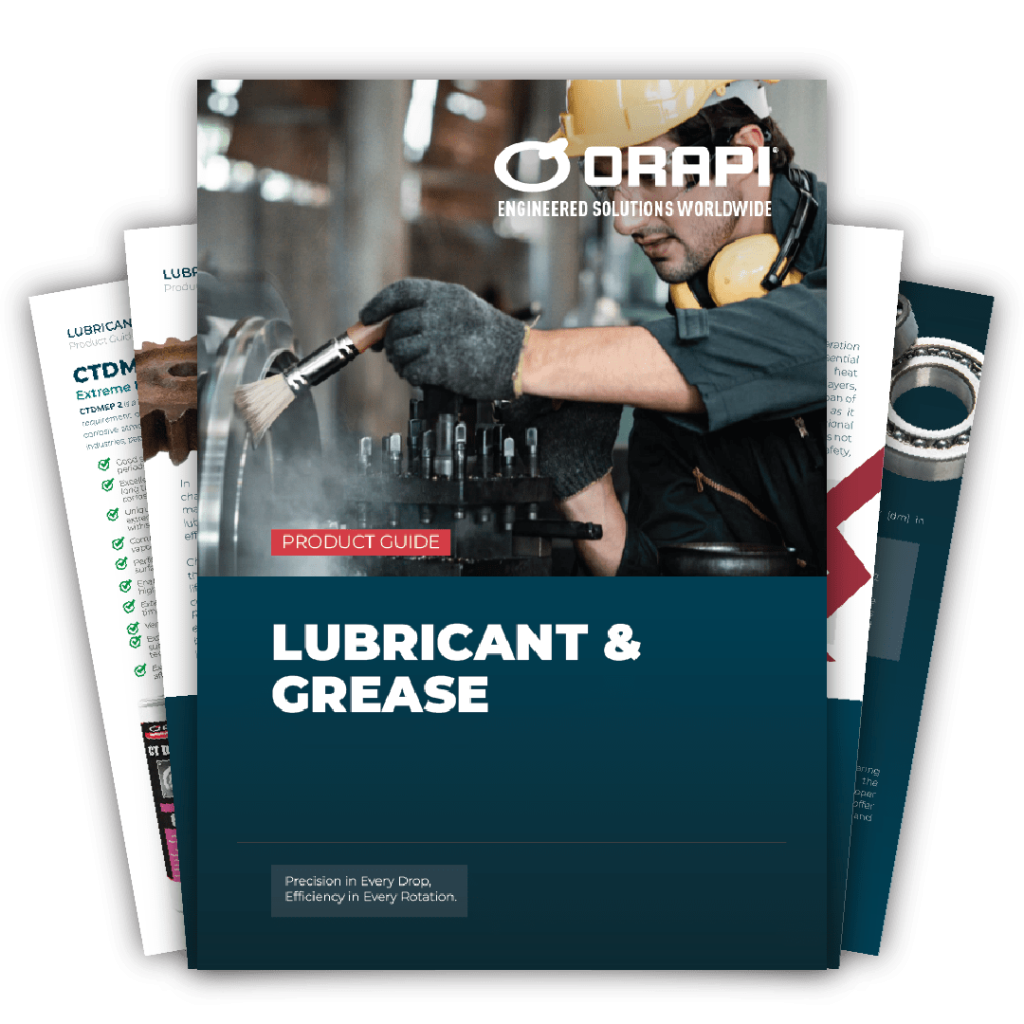